What is an Aluminum Tube?
The extrusion process is the process of forcing an aluminum tube through a mold to give it the desired shape. This technique yields tubes with a variety of applications while guaranteeing accuracy and uniformity. These tubes come in two varieties: seamless and welded, each with special qualities.
Because of their continuous, smooth surface, seamless aluminum tubes are perfect for applications that demand a high degree of structural integrity. However, welded aluminum tubes often design freedom for a range of applications because they are created by joining disparate elements together through welding.
The capacity of aluminum tubes to bend into exact forms and combinations is a crucial feature that helps them suit the needs of several industries, including aerospace, automotive, and construction. Additionally, because aluminum naturally resists corrosion, these tubes guarantee longevity and durability in a variety of applications, making them ideal for settings exposed to moisture or harsh weather.
Different types of Aluminum Tubes
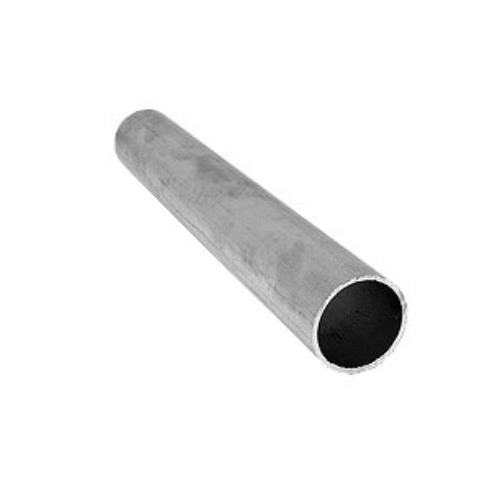
These tubes have a circular cross-section, which provides uniform strength in every direction. In industries like aerospace, automotive, and construction where a smooth, rounded appearance is desired, you’ll find them commonly employed.

These tubes are frequently used because of their square cross-sections, which offer structural integrity. They are frequently used in situations when right angles are required. They are appropriate for your architectural projects, support structures, and frameworks due to their geometric adaptability.

With their rectangular cross-section, these tubes provide a superb mix of strength and compactness. When a certain shape is required for structural or aesthetic reasons, they are frequently used in the manufacturing, fabrication, and construction processes.

Section bars come in a variety of shapes, including T-bars, U-channels, and I-beams, among other aluminum profiles. Their goal is to improve the stability and strength of different structural parts used in construction, industrial, and engineering projects. These bars provide versatility in fulfilling particular load-bearing specifications
Process Used in Aluminum Tube Fabrication

Press bending process is shaping aluminum tubes into the required shape through a press brake. This method works well so it makes basic bends and angles in tubes. It is frequently used in sectors like appliance and automotive manufacturing where repeatability and precision are crucial.

Aluminum tubes are bent round a rotating bend die using a die and mandrel process known as rotary draw bending. This technique is appropriate in applications that require intricate tube shapes because it can bend materials more precisely and complexly. Rotary draw bending is frequently used in industries like aerospace and custom metal fabrication.
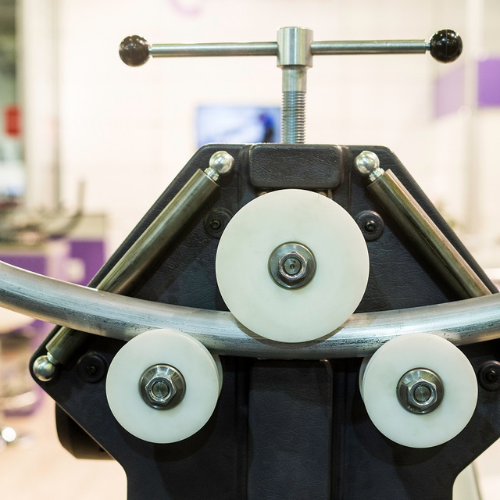
Roll-bending is a process in which an aluminum tube is passed through movable rolls in order to get the appropriate curvative and it is also known as three-roll bending or pyramid rolling. The central roll modifies so it controls the tube’s curvature while the two outer rolls remain stationary. This technique is flexible and can be used to create circular shapes and bends with a large radius. Roll bending is frequently used to create curved sections for handrails, architectural features, and specific kinds of tubing where a continuous, smooth curve is required.

By heating specific regions of an aluminum tube in increasing its pliability, heat-induction bending allows the tube meeting the required shape. Large-radius bends can be made with this technique without sacrificing the material’s structural integrity.
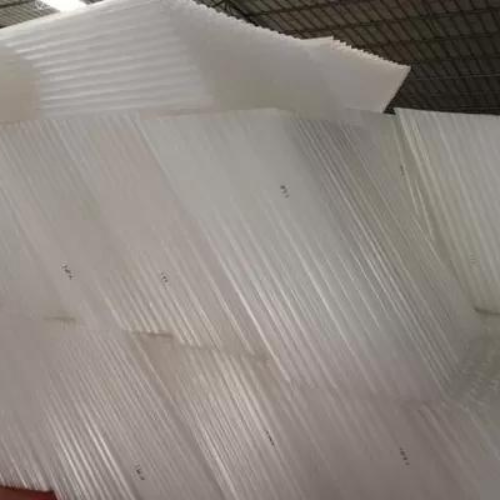
When specialized shapes are needed for particular applications, like art installations or architectural components, hoy-slap forming, also referred to as sand packaging, is a process that involves filling a tube with sand and heat in a malleable temperature.
Most often material used for Aluminum Tube Fabrication
Aluminum Alloys:
The main raw materials used in fabricating aluminum tubes are aluminum alloys. These alloys offer a variety of qualities like strength, corrosion resistance, and malleability. The common aluminum alloys are alloy 1100, 1050, 2024, 3003, 5052, 6061, 7075, 8011
Extrusion Dies:
Extrusion dies are crucial equipment for shaping and producing aluminum tubes during the extrusion process. They are significant since they have a major impact on your tube’s cross-sectional profile. These dies are expertly crafted to ensure consistent features and measurements, guaranteeing accurate results every time. The common extrusion dies are Round Dies, Square Dies, Rectangular Dies, Oval Dies, and Tapered Dies
Welding Electrodes/Fillers:
Welding procedures employing welding electrodes and fillers are used to join aluminum tubes. The strength and integrity of welded joints are enhanced by these materials. The common welding electrodes/fillers are Tungsten Inert Gas (TIG) Welding, Metal Inert Gas (MIG) Welding, Gas Metal Arc Welding (GMAW), Flux-Cored Arc Welding (FCAW), Submerged Arc Welding (SAW)
Bending tools:
Bending tools like roll benders, press brakes, and rotary draw bending machines are used in the fabrication process to shape aluminum tubes. The Common Bending Tools are Manual tube benders, Hydraulic tube benders, Mandrels, Tube Notchers, etc.
Cutting blades:
Using cutting blades, you will accurately cut aluminum tubes to predefined lengths during the fabrication process. You can use a variety of cutting techniques, such as shearing, laser cutting, and sawing, depending on the degree of precision and output required for your project. The common cutting blades in aluminum fabrication are circular saw blades, hacksaw blades, band saw blades, Abrasive Cut-off Wheels, Laser Cutting Machines Plasma cutting Machines, Waterjet Cutting Machines, and shearing machines.
CNC Machining tools:
Lathes and mills, among other CNC (Computer Numerical Control) machining tools, are used to machine aluminum tube components. These tools are made to carry out precise drills, cuts, and other machining operations. The common CNC Machining tools in Aluminum tube fabrication are CNC milling Machines, CNC Lathes, CNC Tube Benders, CNC Drilling Machines, CNC engraving Machines, CNC Deburring Machines, CNC Sawing Machines, CNC Grinding Machines.
Conclusion
The ability to work with aluminum alloys, precise extrusion dies, welding electrodes, and fillers to build strong joints is essential when fabricating aluminum tubes. Cutting blades guarantee exact lengths, tubes are shaped by bending tools, and minute details are added by CNC machining equipment. It’s a complex process where each part and tool counts and the result is aluminum tubes that are specifically designed to meet your needs.