There might be a possibility that you question how Snap Fits perfectly made and how it contributes to ease some problems. This guide will cover Snap fit design and how it can be used to solve problems quickly and simply! In this comprehensive guide, the definition, methods, components, benefits, constraints, and uses of Snap Fit and Snap Fit design will be further explained. So, keep reading!
What is a Snap Fit?
Snap Fit is composed of two pieces that hold together to form a mechanical assembly. It is a simple, economical and rapid product.
Its interlocking elements firmly hold the two pieces together.. With its Elasticity and Flexibility, it eases even the very common situation during assembly.
Snap fit can be any form, e.g hook, bead, or head, depending on its type. However, it has tapered surfaces that can easily adjust for assembly. In order to prevent inadvertent disengagement, snap fittings frequently include retention mechanisms. And also, its locking mechanisms provide additional security whether its undercuts or detent.

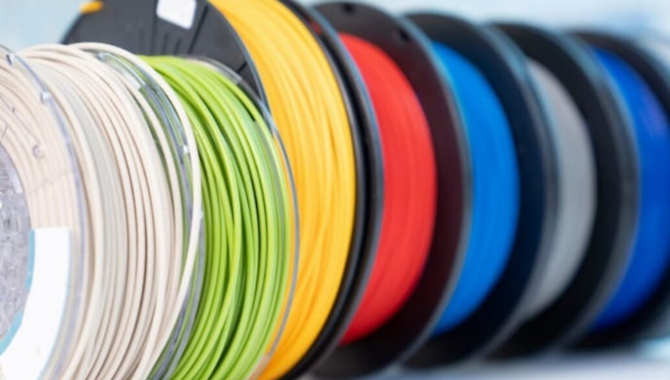
Common Materials Used in Snap Fit Design
The materials that are most frequently used in snap fit design for plastic injection molding are thermoplastics, nylon, ABS, and polycarbonate. These resources were chosen for usage because they have the necessary qualities.
ABS is renowned for its great impact resistance, affordability, and durability in a range of applications. Polycarbonate is a wonderful choice when visibility is important since it provides a nice mix between strength and transparency. The simplicity of molding and adaptability of thermoplastics make elaborate snap fit designs more feasible. Snap-Fit Components can tolerate dynamic stresses and are often more durable due to the strength and flexibility of nylon.
The choice of materials is essential for maximizing the lifetime and functionality of snap fit joints.
Snap Fit Designing Tips
In Designing Snap Fit, there are common factors that should be considered in order to have a durable and flawless final product. Below are some listed tips to be considered:
A. Selection of Material
Make sure to have a material that contains the right balance of strength and flexibility because they are necessary to withstand distortion beyond the elastic limit of the snap fit and to enable the deformation necessary for the snapping process. For the performance of material, environmental factors like temperature and humidity must be considered.
B. Analysis of Tolerance
To account for real-world changes in dimensions, take manufacturing variations and design tolerances into consideration. Analyze tolerances to make sure the parts fit correctly in various manufacturing situations.
C. Distribution of Loads
To guarantee constant stress throughout the snap fit during assembly and use, proper load distribution is crucial. Snap fittings with clever designs disperse forces to avoid hot spots in the system.
Types of Snap Fits/Joints
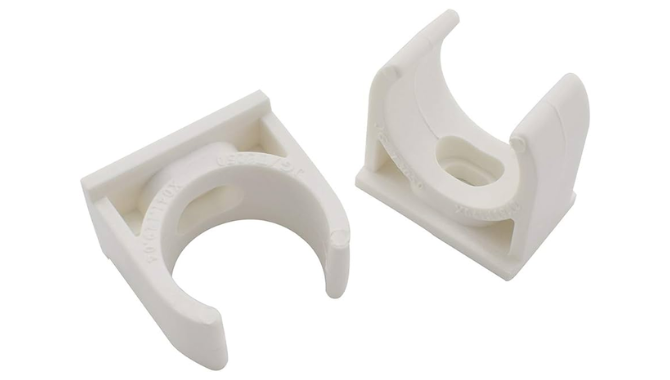
A U-shaped snap fit, which is sometimes referred to as a U-shaped snap feature,is a design element that is frequently employed in product and engineering design to establish a safe and reversible connection between two components. The U-shaped configuration, which is built into one of the components to engage with a similar feature in the mating components, is shaped like the letter “U”.
It has advantages like easy to assemble, reversibility, cost-effectiveness, user-friendly, and applicable to various industries. However, it also has disadvantages like limited ability to support a load, sensitivity tolerance, matters concerning material compatibility, restricted range of movement, danger of long-term deformity.
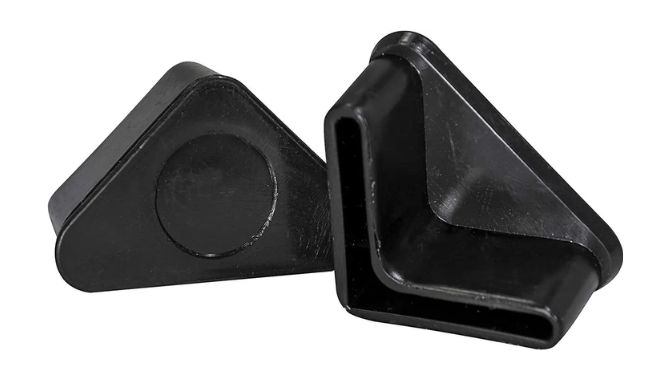
A frequent design arrangement in engineering and product design which is used to securely join two components. This kind of snap fit has an L-shaped geometry and usually involves one component with a projecting tab. The L-shaped facilitates easy construction and disassembly and allows for secure attachment.
It has advantages like the design is simple, easy to assemble, reversible, applicable in diverse industries and cost-effectiveness. But, it also has disadvantages like having limitations in terms of the amount of load, sensitivity to manufacturing tolerances, risk to permanent deformation, range of motion is limited and application-specific.

Torsion Snaps Joints also have cantilever arms with interlocking properties similar to clips which makes it comparable to cantilever snap joints. Nonetheless, a torsional force–typically generated by a spring and bearing–maintains the arm in place.
One must remove the interlocking clip against the spring tension in order to install or disassemble. It’s a straightforward joint with a long lifespan and low failure rate.
Torsion Snaps Joints have advantages also, it has enhanced-load bearing capacity, improved resistance to Axial forces, 360-degree engagement, greater tolerance to misalignment and durability in Heavy-duty applications. On the other hand, it has disadvantages also, like design is complex, cost-production and tooling are high, potential for difficult assembly, and consideration for Material Compatibility.
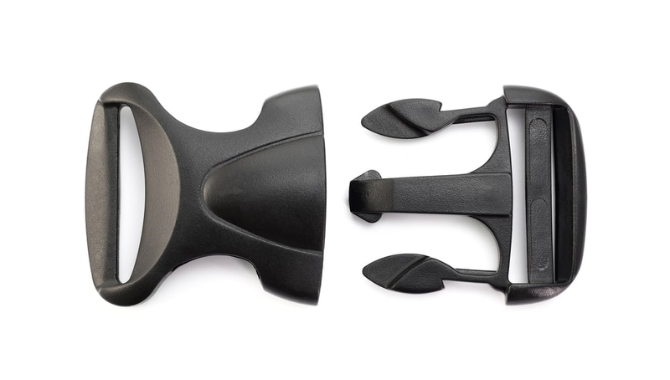
The design of the Cantilever snap Joints is spring-based. It firmly fastens two parts together. One section of the design features many lobes or bumps. On the other side, there are an equal amount of catches.
The lobes snap into position when these components are compressed together. Interference, or ‘bite’ fit, causes them to produce a strong joint. Fillet the cantilever lug base to prevent fatigue and failure of this snap-fit. This lessens the concentration of stress at these locations.
Cantilever Snap Joints do have advantages when in use like the designs are simple, it is easy to assemble, cost-effective production, part counts are reduced and tooling requirements are minimal. However, it also has disadvantages like the capacity of load is limited, sensitivity to materials properties, range of motion is limited, it is not ideal for heavy-duty applications and risks permanent deformations.

An annular snap fit joint is made out of a circular hoop that enlarges when it is pressed into an identical, stiff groove. The annular hoop experiences stress from the expansion, which produces enough frictional force to keep it above the groove structure.
This snap fitting’s consistent stress distribution in circular geometries makes it suitable for high-stress applications. On the other hand, hyperextension is a possibility, and repeated use might cause the snap fit to become progressively looser.
Annular snap fit joints have advantages which are, one-to-one cooperation, equitable distribution of stress, axial and radial stability are improved, adequacy in sealed conditions, and simpleness of assembly. However its disadvantages are the intricacy of the design, increased cost of tools, restricted alignment flexibility, challenging disassembly, and possibility of greater material stresses.
Components of Snap Fit

These are the joint’s interlocking components. Usually, one component has tabs or bulges, and the other has slots or recesses to match.
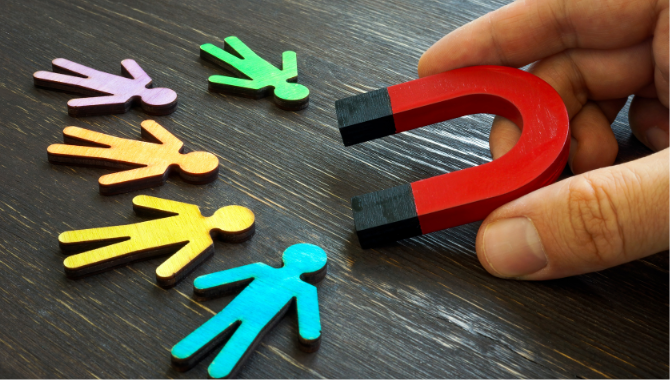
These components aid in maintaining the snap fit joint’s security after assembly. They keep the components from inadvertently coming apart. Features such as undercuts or other types of interference between the mating components could accomplish this.
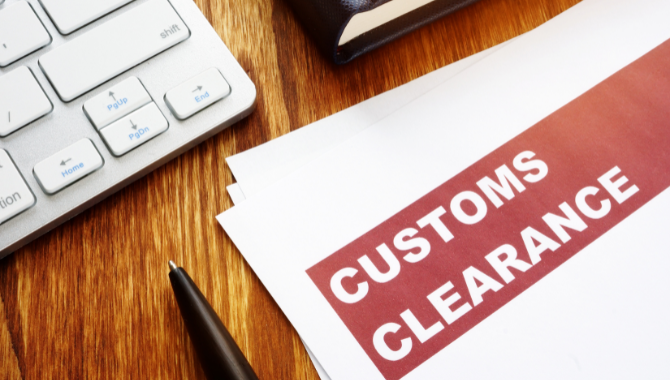
Typically, the snap fit connection is made with a tiny amount of clearance or room to facilitate simpler assembly. It guarantees that the components snap together with ease and without requiring a lot of force.

Snap fittings are highly dependent on the materials’ strength and flexibility. The materials ought to possess sufficient strength to preserve the integrity of the joint while also allowing for a minor deformation to facilitate the snapping motion.

Consider the anticipated differences in dimensions that may arise throughout the production process. It provides for a certain amount of fit flexibility, guaranteeing that the snap fit can still work even if the component’s real dimension differs somewhat from the ideal.
Application of Snap Fit
Snap Fit is an eco-friendly product that is very useful in many applications including snap fasteners, bag latches, tupperware lids, pen caps and more. This can also be applicable in different processes like prototyping and snap fit for 3d printing designs.
Common Problems and Limitations of Snap Fit Design
Snap fit design examples frequently encounter difficulties like stress concentration, which results in possible weak points as forces are concentrated on particular areas. A steady deformation over time known as creep might make the fit less secure. Repeated stress can lead to fatigue loading and repetitive loading failures, which can affect long-term durability. Tolerance problems may occur and compromise the accuracy of the fit. One disadvantage of the complex production process is that it adds to the complexity of manufacturing. Although snap fittings are more convenient, they are often weaker than permanent joints and are prone to breaking.
Conclusion
The dynamic and adaptable field of snap fit design for sheet metal provides innovative solutions to an extensive variety of industries. Through an understanding of snap fit’s characteristics, features, and applications as well as typical problems, designers can use this technology to produce effective, affordably priced, and user-friendly solutions. Now is the time to let your inspiration come to life and guarantee a smooth creative process! Request snap fit design pdf for more information.