From roll cages and bicycle frames to complex medical devices metal tubes with distinct shapes and sizes are the lifeblood of your modern equipment.
However, to convert these raw tubes into the well-shaped and sized components you need, tube fabrication is necessitated.
This guide explores fundamental processes in tube fabrication process – let’s dive right in:
What is the Tube Fabrication Process?
Tube fabrication is an operation that seeks to customize the size and form of your straight metal tubes.
This process can exploit varying shape-altering methodologies with the most popular methods being welding and bending. You can utilize tube fabricating services to generate chassis, metal frames, and other essential components.
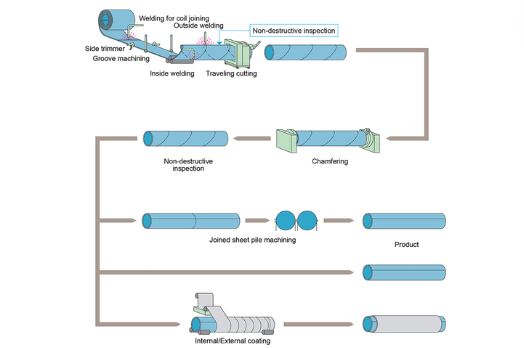
Types of Fabrication Techniques
Tubing fabrication gives you the essential conduits that allow you to fulfill numerous functions including ferrying liquids and gases. To generate your desired metal tubing, you can exploit either of the underlying tube fabrication processes.
Mandrel Tube Bending
This tube fabrication process utilizes a solid rod to manipulate the shape form of your metal pipe or tubing. This rod, which is typically referred to as the mandrel is embedded inside your metal tubing and it ensures that your tube comes out with the perfect shape.
Additionally, it thwarts wrinkling and collapsing. Tube bending technique comes in handy when producing metal tubing for exhaust systems and roll cages amongst other essential industrial constituents.
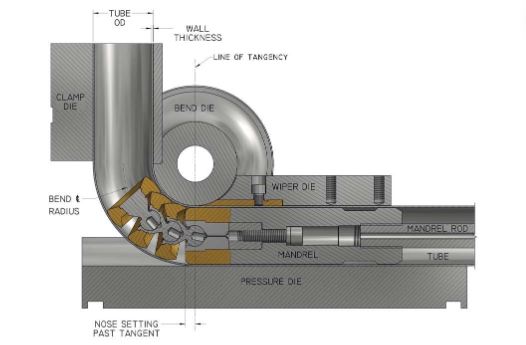
Advantages
- Improved Tube Bending: This technique will reward you with fabricated tubes characterized by wrinkle-free bends and smooth finishes.
- Repeatability: Using a mandrel bending machine, you can regulate the bend angle and this translates into high-quality bent tubes with consistent bends.
- No Need for Finishing Operations: Mandrel tube bending delivers wrinkle-free tubes, meaning you do not have to incur the cost of undertaking finishing operations like smoothening.
Tube Hydroforming
Tube hydroforming allows you to come up with metal tubes characterized by complex geometries and near-perfect shapes.Hydroforming technique relies on high-pressure fluids. To shape your metal pipe, you are simply required to place it in a die set before injecting your hydraulic fluid.
This pressurized hydraulic liquid consequently forces your tubing to expand thus manipulating its shape and size. Tube hydroforming will come in handy as you look to generate suspension components and bicycle components among other metallic components.
Advantages
- Uniform Tube Thickness: Tubes fabricated via hydroforming exhibit an even wall thickness. This ensures that your tube’s entire structural integrity is evenly strong.
- Complex Geometries: This technique opens up opportunities for imparting complicated shapes on your tubes. You cannot impart some of these shapes using other fabrication processes.
Tube Swaging
Tube swagging as a fabrication process permits you to come up with well-shaped tubes or pipes characterized by reduced stress concentration points. It requires you to utilize a swagging machine, which exploits dies to manipulate your tubing’s diameter.
With tube swagging, you can either expand or shrink your metal tube’s diameter. To expand its diameter, your die will exert pressure from the inside, outwards. However, you must carefully monitor the swaged area during the fabrication process to avert wrinkling.
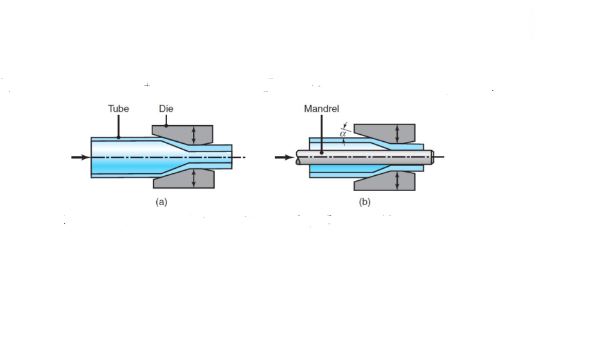
Advantages
- Improved Fit:Swagging leaves your tubes with a befitting attachment area making it easier to link your tubes to other essential components.
- Increased Strength: This process compacts materials around the fabricated area, making it stronger and more resistant to force.
Spinning Tubes
Spinning is a tubing fabrication technique that attempts to install decorative features on your metal tubing. Spinning fabrication accomplishes this by generating tapered ends using distinct spinning tools such as specialized lathes. Once you bring your tubing into contact with the spinning tool, the patterns on its surface are likely to be transferred onto it.
You can regulate the speed and pressure of your spinning tool and this will help you control the ultimate shape of your tubing. However, when using this technique, you must be prepared to employ additional finishing processes including polishing.
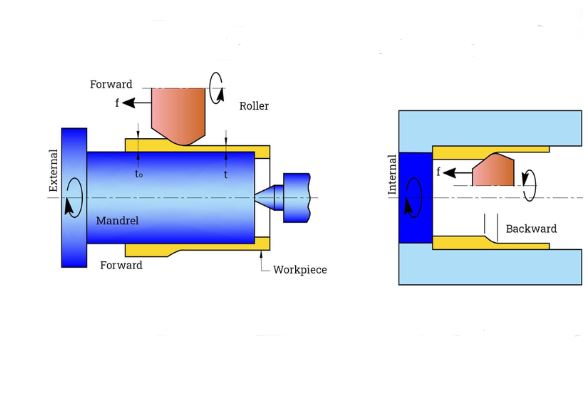
Advantages
- High Precision: You are guaranteed high-quality tubes due to the precision spinning guarantees. Your fabricated tubes will demonstrate smooth surface finishes and dimensional accuracy.
- Versatility: Using this technique, you can impart varying shapes or patterns onto your metallic tubes ranging from simple to sophisticated geometries.
Expanding Tubes
Expanding fabrication is typically exploited impart joining parts on special tubes including plumbing pipes and HVAC tubes. This technique relies on expansion tools such as mandrels to enlarge designated ends or points of your metal tubing. Once the expansion tool is inserted inside your tube, it causes your tube to expand outwards.
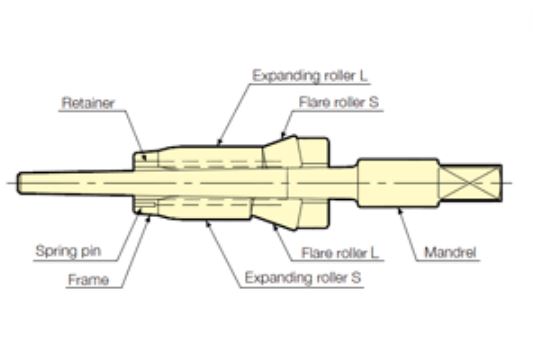
Advantages
- Enhanced Tube Strength: The joint created by enlarging your tube can resist considerable force as well as certain environmental elements.
- Leak Resistance: The expanded end can accommodate mating components more comfortably, meaning you are less likely to suffer from leaking.
Beading Tubes
This tubing fabricating process attempts to impart ridges of specified diameters on designated areas of your metal tubing or pipe. These raised points are typically referred to as beadings and they mainly act as stopping points for your metal components. You can utilize these beadings to securely fit other accompanying tubes or components.
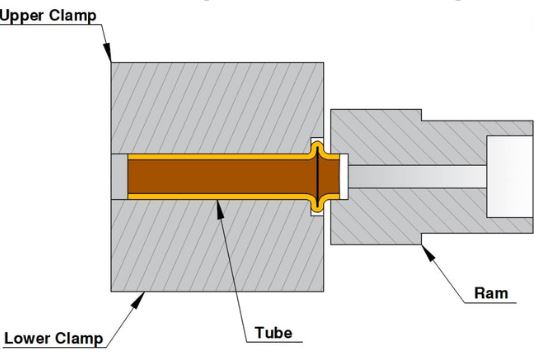
Advantages
- Leak Resistance: If you intend to use your tube as a conduit for certain products like liquids, the beads imparted by this technique will act as barriers that will prevent leakage.
- Better Alignment: The beads on your tube can also act as markers, which will help you position secondary fittings along your metal tubing.
Flaring Tubes
Flaring tubing fabrication seeks to generate metal tubes with flared ends thus making it easier for you to link other components. The tube fabrication machine utilized to generate flared tubes or pipes features a flaring cone and die. Inserting the flaring cone into your tube and consequently pressing it results in the creation of a flannel-like shape. This technique allows for secure connections and elevated tube strength.

Advantages
- Secure Connection: Flaring generates flared ends, which make it possible for you to achieve leak-free joints.
- Strong Sealing Capability: The tube endings created by this technique allow you to connect your tube to essential components such as fittings and gaskets.
- Improved Strength: The part of your tube fabricated via flaring often exhibits more rigidity. This means that you can subject your tube to heavy loads, without having to worry about breakages.
CNC Tube Cutting
This technique is presently subject to immense exploitation thanks to its ability to accomplish repeated tubing fabrication results. You first place your metal tubing into the CNC tube cutting machine where it is securely clamped using chucks or rollers.
Secondly, you are prompted to program the specific cutting parameters you expect the machine to execute. The machine then proceeds to execute the commanded functions with utmost accuracy thus ensuring that your design specifications are met.
Advantages
- Precision: This process depends on pre-programmed machines, which guarantee precise tube fabrication. This even permits you to achieve repeatable cutting results.
- Higher Productivity: When utilizing a CNC tube cutting service, you are likely to fabricate more metal tubes due to the high automation level.
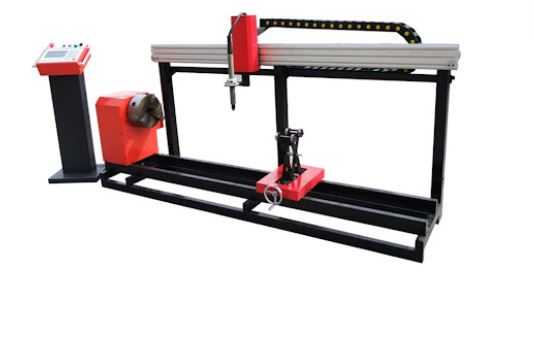
Welding Tubes
Welding simply allows you to link or combine two or more metal tubes thus leaving you with a longer or bigger component. It involves the use of heat to melt the ends of certain points of your tubes. This makes it easier to fuse the melted ends. You can exploit either of the following welding fabrication processes:
- Metal Inert Gas Welding
- Tungsten Inert Gas Welding
- Shielded Metal Arc Welding
- Flux-cored Arc Welding
To arrive at a welding technique that suits you best, you must look at the thickness of your tubes as well as how strong you want your linked points to be.
Advantages
- Permanent Bonds: Welded bonds or joints are nearly impossible to break, meaning you can utilize your welded tube to carry out heavy-duty operations.
- Cost-Effective: Welding simply involves the use of heat, which is comparatively one of the cheapest joining techniques.
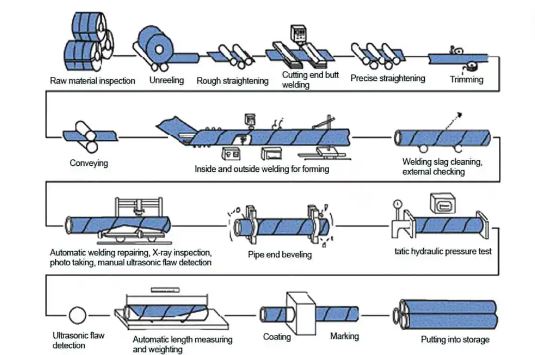
Draw Bending Tubes
Draw bending fabrication is principally utilized in high-production tube fabrication operations due to the control it offers you over the bend radius. This technique often utilizes a mandrel, however, the mandrel deployed must be slightly smaller than your tube diameter.
When using this fabrication technique, you are advised to keenly monitor the bend radius and angle. This will help you achieve your coveted bend geometry. Draw bending also guarantees you minimal distortion or wrinkling thanks to the utilization of mandrels.
Advantages
- Minimal Distortion: If your tube has relatively thinner walls, using this technique guarantees that it will resist breakages during the fabrication process.
- Uniform Bends: This methodology consistently delivers well-fabricated metal tubes irrespective of the tube thickness and material.
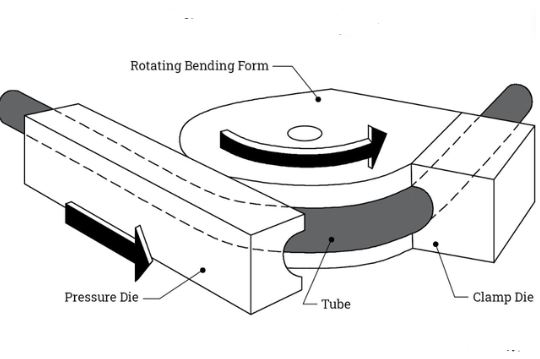
Flattening Tubes
Flattening simply manipulates your tube’s shape to resemble a horizontal or even surface. This is crucial for components destined to be deployed in certain applications, for instance, tubes meant to be deployed as mounting surfaces. This fabrication technique exploits flattening machines, which often come equipped with presses and rollers.
Advantages
- Amplified Surface Area: Flattening gives you metal tubes with a comparatively larger surface compared to irregularly shaped tubes. This gives you a bigger attachment area.
- Enhanced Rigidity: This technique gets rid of the bending in your tube or pipe and this makes it more resistant to deformation even when holding heavy weight loads.
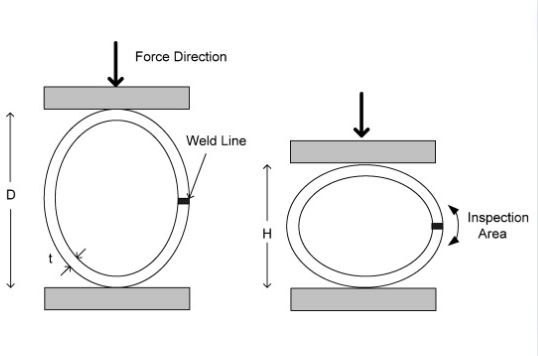
Tube Coiling
Tube coiling is primarily utilized to fabricate the form of metal pipes into helical coils, which are essential in systems such as heat exchangers. This process subjects your tubes to mandrels or rollers that carefully bend them into a cone shape. Typically, this process is accompanied by secondary processes such as trimming and surface treatment.
Advantages
- Better Heat Exchange: This technique delivers coiled tubes characterized by increased surface areas, making them more friendly to heat transfer.
- Space-Efficient: The finished coiled tubes have a comparatively more compact design meaning you can fit them into constrained spaces.
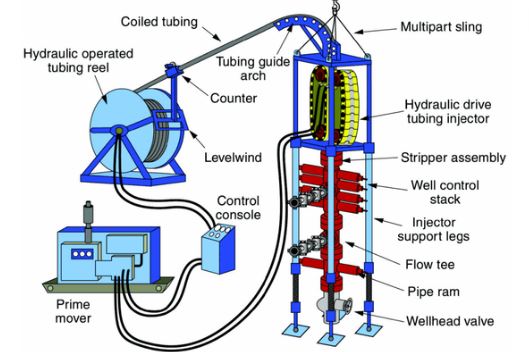
Tube Fabrication Machines
Metallic tubes are characteristically intense and rigid meaning you can hardly bend them by hand. To fabricate their shape, you will require specialized equipment, which include;
- CNC Roll Benders: These tube fabrication machines are often utilized to manipulate the formation of metal tubes in high-volume operations. They depend on computer-controlled rolling pins, making them highly accurate and reliable.
- Compression Tube Benders: These tube bending machines are specialized to distort the shape of your metal tubes using force. They consist of a clamp and die, which are the primary components responsible for bending tubes. They mainly favor thin-walled pipes and tubes.
- CNC Tube Cutting Machine: These machines come equipped with distinct cutting devices all controlled by CNC software. Thanks to their CNC-controlled lasers or cutting blades, these tube cutters often achieve unrivaled precision.
- End Tube Forming Machines: These fabrication machines are uniquely engineered to shape designated ends of your metal tubes. End tube forming machines typically execute either of the following fabrication techniques;
- Flaring
- Swaging
- Expanding
They help you create customized tube endings making it easier for you to connect your tubes to other fittings or tubes.
- Tube Laser Cutting Machines: These machines exploit the power of lasers to help you impart varying patterns or shapes to your tubes. Tube laser cutters accommodate a more diverse range of metal materials, unlike conventional tube fabricating machines.
- Electric Tube Benders: These tube bending machines thrive in medium-sized tube fabrication projects. They are renowned for exploiting electricity to reduce your physical workload. Electric tube benders often achieve impressive tube fabricating accuracies and are quite affordable.
- Manual Tube Bending Machines: Manual tube benders require you to exert some level of physical force for tube bending to occur. As such, their use is limited to small-sized operations and metal tubes that are relatively softer.
- Hydraulic Tube Benders: These bending machines have been known to thrive in industrial tube fabrication due to their ability to handle high volumes of heavy-duty pipes. They exploit hydraulic pressure, which is quite effective in manipulating the shape of your metal tubes.
- Rotary Draw Bending Machines: These tube fabricating machines will suit you better when you are looking to impart intricate shapes on your thin-walled tubes. They come with a mandrel, which ensures precise bending whilst thwarting material collapse.
- Tube Hydroforming Machines: Tube hydroforming machines rely on specialized molds and highly pressurized liquids to distort your tube’s shape. They are quite prominent in the automotive industry since they can impart complex geometries.
- Tube Welding Machines: Tube welding machines simply fabricate your tubes’ shape and size by joining them. They primarily rely on heat, which enables them to achieve strong and near-permanent linkages.
Tube Fabrication Applications
Each industry reliant on metal tubes needs them configured in unique shapes and dimensions. This has prompted an increase in the demand for tube fabrication machinery mainly among the following industries:
- Automotive Industry: Tube fabrication is essential in generating essential automotive components like motorcycle frames and car exhaust systems.
- Construction Industry: Construction necessitates numerous systems, which feature metal tubes heavily. Tube fabrication helps shape plumbing tubes and tubes necessary for HVAC systems.
- Oil and Gas Industry: Tube fabrication also provides the oil and gas industry with perfectly sized and shaped conduits for transporting oil and gas. It allows these industries to expand or swag tubes thus averting leakages.
- Aerospace Industry: Thanks to tube fabrication machines, distinct aircraft components can be generated. They include landing gears, fuel lines, and plane frames.
- Medical Equipment Manufacturing: Tube fabrication makes it possible to achieve intricate patterns on medical equipment such as diagnostic machines.
- Agricultural Industry: The vast majority of contemporary farming equipment is made from uniquely bent or shaped tubes. These tubes are generated with the help of tube fabrication machinery.
- Consumer Electronics Manufacturing: Modern consumer electronics such as computers and cooling systems rely on metal tubes shaped and cut with the aid of tube fabrication equipment.
- Fitness Equipment Manufacturing: Fitness equipment such as lifting weights and treadmills rely on metal tubes customized via tube bending and cutting.
- Power Generation Industry: Metal tubes deployed in power lines and cooling systems among other power systems are shaped and fabricated with the help of tube benders.
Conclusion
Thanks to tube fabrication, you can now access metal tubes with varying properties including swagged or flared ends. These tubes ultimately form the building block of the essential infrastructure and products we utilize daily.