Weld Line Meaning
A weld line, also called a knit line, is the point in the molding process when two flow fronts converge. This line usually appears when these fronts cannot “weld” or blend smoothly. Weld lines, which are frequently observed around holes or blockages, are a sign of weak spots in the molded component.
Why Weld Lines Occur in Injection Molding
Velocity: The resin will flow through the mold moderately quickly and gradually. This implies that the fronts might not cool simultaneously.
Contamination: The resin will not flow readily through the mold if it contains contaminants.
Release of excess mold: If the mold is too much, you may need to apply additional pressure to get it released by the machine.
Apply pressure: If there is not enough pressure to drive the flow and combine again, this can produce a large weld line.
Warmth: An early start to solidification may occur if the temperature is not raised enough.
Design of the mold: A badly constructed mold may cause weld lines to appear in different places across your design.
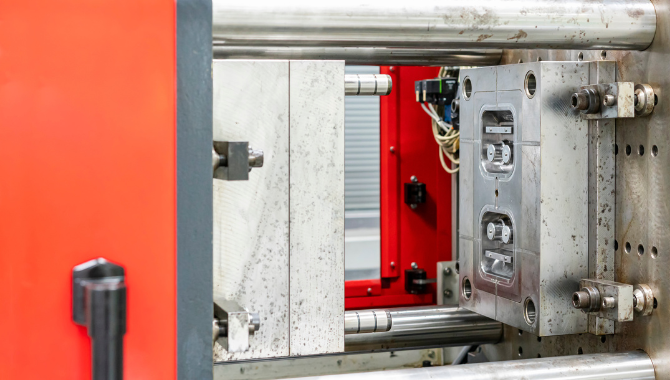

The Reasons Behind Avoiding Weld Lines
Vulnerability
The weakest point on your part is typically the weld lines. As a result, the material can separate from such an area with ease. The weakness brought on by the weld lines may prevent the item from properly fulfilling its intended function if it is intended for one that calls for high strength.
Distorted Appearance on the Surface
Knit lines could distort your design’s appearance. Regardless of the amount of work you put into making the design visually appealing, one knit line could be the focal point that causes the pattern to become distorted.
Weld Lines and Meld Lines Difference
Weld Lines
What is weld line in plastic parts, a weld line is created when the thin frozen layers ahead of each flow direction come together, melt, and then re-freeze with the remaining plastic.
Meld lines
Weld line meeting angle, a meld line is formed when two flow fronts cross at an oblique angle.
This enables the plastic molecules to be orientated more consistently than what would typically happen once a weld line occurs. This figure shows the length of the portion where a melt line forms.
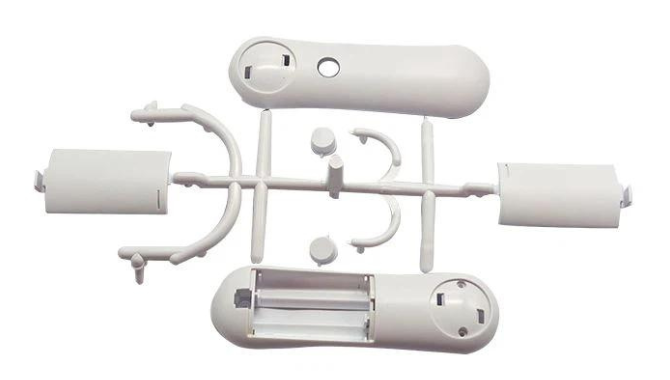
Guidelines on Preventing Weld/Knit Lines in Injection Molding of Plastic the Properties
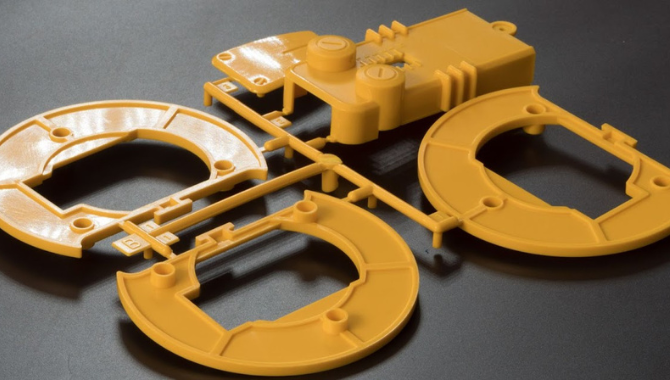
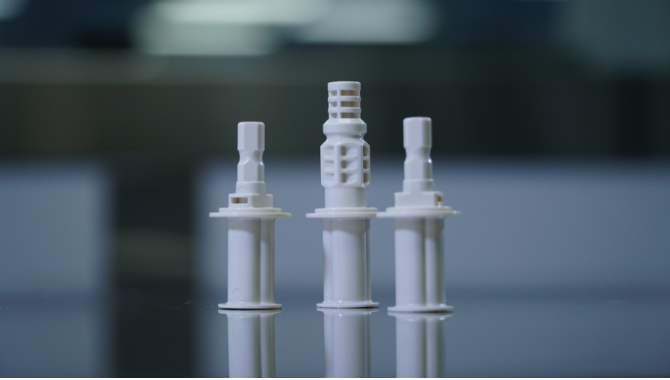
Modify The Component Layout
This can be accomplished by thickening the walls. In addition to ensuring a higher melt temperature, this will aid in the passage of pressure.
Change The Molding’s Layout
By making the gate and runners larger, you can change the mold’s design. Eliminate any trapped air in the metal injection molding of the weld line.
Modify The Shaping Circumstances
Weld line in injection molding: modifying the molding conditions is another technique for removing weld lines from plastic injection molding. Temperature, injection pressure, and speed are the conditions.
Weld lines are more than merely an unsightly flaw in the plastic, even though they are often barely perceptible at all.
Anytime there is a separation between the plastic, whether it be due to air or a plastic additive, a weak spot is formed because the polymers don’t meet to bridge the gap.
When molten plastic material comes into contact with something or diverges around a feature inside the mold cavity, weld line in welding are created.
The two flow fronts then meet and merge at this point, where the material rejoins.
Melt temperature, injection speed, material viscosity, mold design, and the presence of inserts or other features in the mold are some of the variables that affect the creation of weld lines.
Reduced strength and durability can result from weld lines weakening a plastic part’s structural integrity. Also, they could result in cosmetic flaws in the part’s look.
How to reduce weld line in injection molding, weld lines are difficult to completely remove, however, they can be reduced in frequency by maximizing the molding parameters, employing sensible mold design techniques, and choosing the right materials.
Several variables, including injection speed, melt temperature, and mold design, must be adjusted to minimize weld lines.
Weld line development is more likely to occur in products with elaborate patterns, thick sections, or complex geometries.
It might be difficult to remove or repair weld lines after manufacturing because they are an integral part of the molding process.
Minimizing weld lines is mostly dependent on proper mold design, which includes part geometry consideration, venting, and gate position.
To find weld lines in completed plastic items, non-destructive testing techniques like X-rays and ultrasounds can be used in addition to visual inspection.