Metal components are welded together using projection welding, a resistance projection welding technique that concentrates heat at specific locations called projections. The purpose of these projections is to produce localized heat on the workpieces, which causes the materials to melt and bond. Because of the technique’s accuracy and efficiency, which guarantee robust and long-lasting welds in a variety of applications, it is widely employed in the industrial industry.
Types of Projection Welding
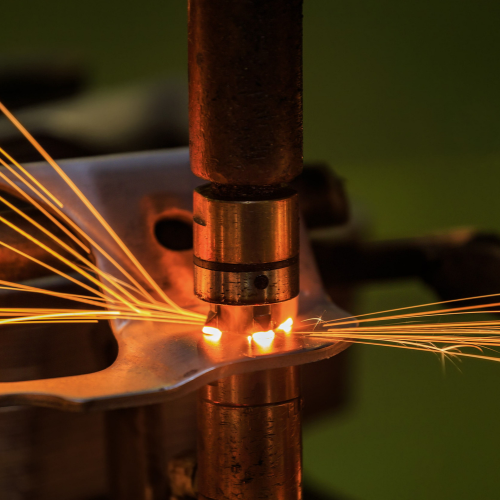
Spot projection welding is the process of welding at a particular location where a projection exists on the workpiece.

A continuous line of projections is seen on the workpieces during seam projection welding.
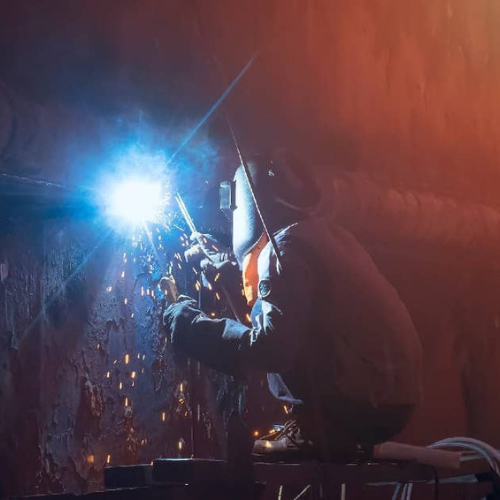
When using grid projection welding, one or both workpieces have a pattern of projections placed in a grid or matrix.

Securing a flange or lip from one workpiece to a flat surface on another is the process of projection welding.

To attach components having raised or embossed features, embossed projection welding is utilized.
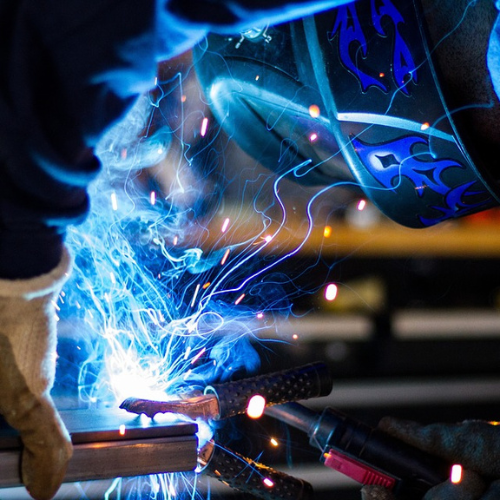
When utilizing upset projection welding, a welding current is passed through two or more projections on the workpieces that come into contact.

A form of projection welding called percussion welding occurs when the projections collide simultaneously with the application of the welding current.

Flattening projection welding is the process of bringing two flat workpieces with projections into contact.
The Projection Welding Process



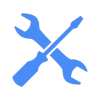



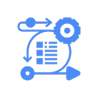


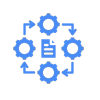
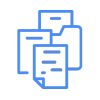
The Advantages of Projection Welding
Increased Output: The technique makes it possible to finish multiple welds at once, which raises industrial output.
Extended Life: Due to their reduced heat and pressure usage throughout the welding process, projection welds are more durable than spot welds.
Adjustability: The projection welding technique is easily adapted to function with a range of parts and components by modifying its settings.
Utilization Ease: Multiple welds can be completed simultaneously when using projection welding, however, this requires highly automated equipment.
Neat Appearance: By focusing the point of contact on one side and using less force, projective welding reduces surface imperfections at the welded seam and improves surface smoothness.
More Intimate Welding: Because each junction is under less pressure when projection welding equipment is employed, welds are spaced closer together.
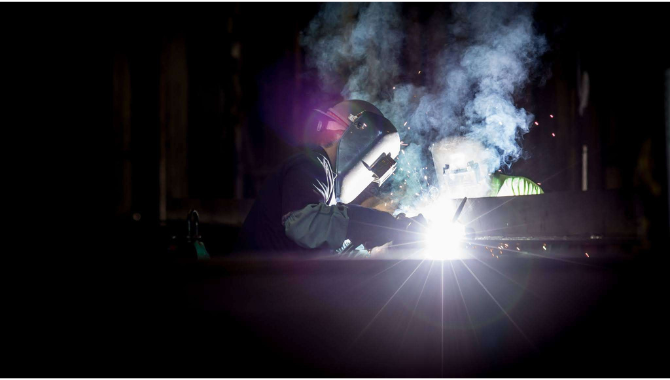
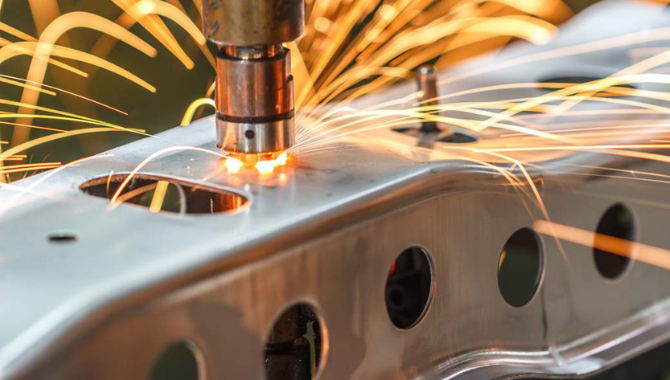
Projection Welding Applications
Automobile – Bolts, nuts, and screws are examples of fasteners that can be joined to flat surfaces via projection welding.
End-user Products – The fasteners in consumer items including fans and fan covers, furniture, and household appliances are secured by manufacturers via projection welding.
Establishment – Thick plates, hollow metal doors, and metal panels are just a few of the construction-related items that are produced using projection welding.
Mechanical – In mechanical equipment, projection welding connects coverings, crossing wires, and fasteners to bars.
Semi-Conductor – Projections welds’ tight fit is ideal for hermetically sealed semiconductor equipment since it seals out gases and air that could hinder the equipment’s functionality.
Particularities Between Projection Welding vs Spot Welding
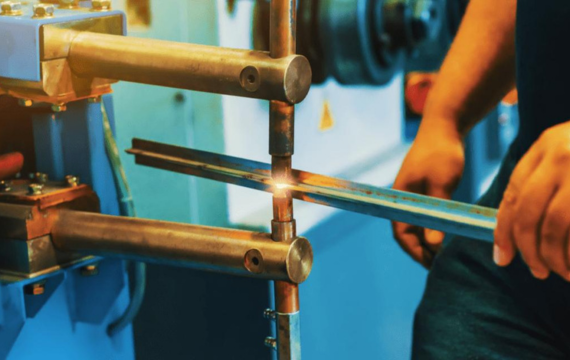
- Since projection welding produces a weld with less heat and pressure, it is more beneficial for thick metal components and items that need an extraordinarily strong junction.
- Because projection welds are less noticeable than spot welds, the finished product could seem nicer.
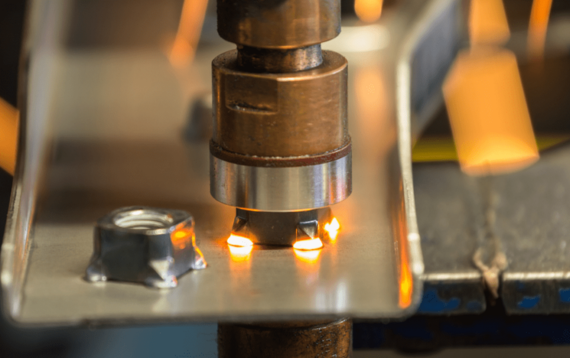
- The most used type of welding is spot welding, which differs from projection welding in a few key areas.
- This method is usually used to link huge metal sheets welding or parts together. It involves flowing metal currents along the junction.
Projection welding machine helps work with a variety of metals due to its adaptability, including:
- Aluminum
- Stainless steel
- Carbon steel
- And other alloys.
Projection welding works effectively in large-scale manufacturing.
This method is quick and effective, which makes it perfect for companies that need a lot of welded parts.
There are several shapes that projections can take, including circular, rectangular, and other types.
To improve consistency and efficiency in the welding process, projection welding is indeed easily automatable.