In this guide aluminum alloys will be discussed in depth focusing on properties, types and uses. Aluminum and its alloys are popular materials in many engineering parts fabrication processes.
What is Aluminum Alloy
Alu alloy refers to a “compound material” consisting of aluminum metal and other elements to improve performance characteristics. Other elements many include copper, magnesium silicon or zinc, just to mention a few.
Alloys of aluminum have exception properties including better corrosion resistance, improved strength and durability, just to mention a few.
These find use in a wide range of industries, including automotive, marine, construction, and electronics.
How Aluminum and Aluminum Alloy Compare
Aluminum is a naturally occurring element with excellent properties like high strength-to-weight ratio, corrosion resistance and being lightweight.
Usually, when referring to aluminum alloys, it basically implies a material with other elements, apart from alu material.
The metal materials are combined in varying proportions depending on the desired end properties and use.
Here is a complete comparison between these two aluminum materials:
Aluminum | Aluminum Alloy | |
Content | Is a pure metal | Contain aluminum in combination with other elements |
Properties | Has relatively exceptional properties such as strength, hardness, ductility and corrosion resistance. | Can be designed to improve on the individual properties of pure aluminum depending on use. |
Cost | Generally cheaper than aluminum alloys. | Can be higher and depends on the type and amount of alloying elements. |
Applications | Finds general application such as in food packaging and household items. | Used in more specific applications depending on the desired property such as durability and corrosion resistance in aerospace applications. |
More resources:
- Aluminum – Source: Wikipedia
- Aluminum Alloys – Source: Science Direct
Properties of Aluminum Alloy
Physical Properties
Aluminum Alloy Density
When it comes to density, there is a variations. At some point, the aluminum manufacturing process.
Generally, these alloys have a lower density than other metals like steel and copper, ideal for applications requiring lightweight materials.
The density of most aluminum alloys ranges between 2.5 g/cm³ to 3.0 g/cm³. The densities of aluminum alloy series are summarized below:
ALUMINUM ALLOY SERIES | DENSITY |
1000 Series | 2.70 – 2.71 g/cm3 |
2000 Series | 2.58 – 2.89 g/cm3 |
3000 Series | 0.0208 – 2.75 g/cm3 |
4000 Series | 2.65 – 2.92 g/cm3 |
5000 Series | 0.0160 – 2.84 g/cm3 |
6000 Series | 2.68 – 2.92 g/cm3 |
7000 Series | 2.72 – 2.89 g/cm3 |
8000 Series | 2.54 – 2.74 g/cm³ |
Aluminum Alloy Color
They are silver-gray while showing some metallic shine. However, this color can vary depending on the alloy type, manufacturing process and surface treatment used.
Surface treatments such as anodizing, painting, or powder coating can color aluminum alloys. The surface treatment can be can be dyed in a wide range of colors, including black, blue, red, and green.
Aluminum Alloy Microstructure
The microstructure of aluminum alloys plays a crucial role in determining their mechanical and physical properties. The alloying elements such as copper, magnesium and zinc alter the microstructure of the aluminum contributing to the alloy’s properties.
While aluminum’s crystal structure is face-centered cubic (FCC), alloying elements create different crystal structures. For instance, when utilizing manganese as an alloying element, it takes up a hexagonal close-packed (HCP) structure.
Alternatively, aluminum alloys can be described as fine-grained to coarse-grained structures at a macroscopic level. At the microscopic level, aluminum alloys tend to have a dendritic or equiaxed grain structure, depending on the casting process used.
Chemical properties
Corrosion Resistance
Aluminum and its alloys are popular for superior corrosion resistance. Usually, there is a thin protective layer that forms on its surface.
By adding other alloying elements, the final product has the best corrosion resistance properties.
Reactivity
Aluminum alloys highly react with substances such as acids and alkalis and even metal like steel causing galvanic corrosion. However, reactivity is checked by the addition of corrosion resistant elements like copper and magnesium forming protective films.

Aluminum Alloying Elements
Looking at the different alloying elements in aluminum, we have:
- Copper: it makes the alloy resistant to both cracking and corrosions. Of course, this is alongside improved hardness and strength.
- Magnesium: Magnesium augments aluminum alloys’ strength, ductility, and corrosion resistance especially in marine environments.
- Silicon: Adding this element to aluminum improves the resulting alloy’s resistance to thermal fatigue, strength, ductility, and ability to cast.
- Zinc: When you combine this element with aluminum, you improve resistance to stress corrosion cracking and strength.
- Manganese: Contributes to better strength while improving corrosion resistance properties.
- Nickel: Adding nickel to aluminum enhances strength and toughness at low temperatures.
- Iron: Ensures better strength and hardness
Aluminum Alloy Chemical Formula
The chemical formula of aluminum alloys are alloy specific and contingent on the elements added. A four-digit numbering system is used to designate aluminum alloys indicating the percentages of the alloying elements present.
Typically, the first digit represents the major alloying element, while the second digit indicates the alloy modification, e.g. purity or processing. Again, if you want to learn more about the specific Alu alloy and classification for modification, you look at the 3rd and 4th digits.
A good example is the 6061-T6 consisting of:
- Aluminum (97.9%)
- Magnesium (1.0%)
- Silicon (0.6%)
- Iron (0.28%)
- Copper (0.2%)
- Zinc (0.1%)
- Titanium (0.1%)
It can also be expressed as Al-Mg-Si-Cu based on the major alloying elements.
Mechanical Properties
Aluminum Alloy Tensile Strength
There are different aluminum alloys constituting different elemental composition. Consequently, you find the tensile strength of aluminum alloys varies depending on the specific alloy and its composition.
Unlike steel, aluminum alloys is characterized by low tensile strength. Though, it is a known lightweight material.
To improve the tensile strength, the Alu alloy has zinc, copper and magnesium among other elements.
It is worth noting that the processing conditions used on aluminum alloys such as heat treatment and cold working, affect tensile strength.
One of the aluminum alloys with a high tensile strength is 7075-T6 clocking about 572 MPa containing zinc as the primary alloying element. Other aluminum alloys such as 6061-T6 and 2024-T3 have tensile strength values of 276 MPa and 470 MPa respectively.

Aluminum Alloy Strength-to-Weight Ratio
Strength-to-weight ratio measures a material’s strength relative to its weight and is a key consideration where weight is a critical factor.
Aluminum alloys have different strength-to-weight ratio depending on factors such as alloy composition, processing method and heat treatment. Some common aluminum alloys with
The 7000 series aluminum alloys exhibit the strongest strength and weight performance finding use in aerospace and military applications.

Elastic Modulus of Aluminum Alloys
The modulus of elasticity or Young’s modulus characterizes a material’s resistance to deformation under stress. The structure of aluminum alloys is one of the important factors that influences an alloy’s modulus of elasticity.
Aluminum alloys have a relatively high modulus of elasticity ranging from approximately 62 GPa to 140 GPa.
Aluminum Alloy Poisson’s Ratio
The property of Poisson’s ratio characterizes the deformation behavior of a material and differs among aluminum alloys depending on composition. Aluminum alloys have a Poisson’s ratio ranging from 0.30 to 0.35.
6061 is an aluminum alloy commonly used in structural applications and has a Poisson’s ratio of approximately 0.33. Contrarily, 7075 aluminum alloy used in aircrafts and other highly sensitive applications has a lower ratio at about 0.32.
Fatigue Strength of Aluminum Alloy
Fatigue strength describes a material’s resistance to repeated loading and unloading cycles. They have high fatigue strength which is contributed by the corrosion resistance and high strength to weight ratio.
However, the fatigue strength varies with application and constitution with high value alloys having higher fatigue strength values. 7075-T6 aluminum alloy, for instance, is rated at 280 MPa in uniaxial loading at room temperature.
The fatigue strength of aluminum alloys can be affected by the stress levels and the frequency and duration of loading cycles. Other factors like presence of defects and environmental conditions notably temperature and humidity are also influential.
Aluminum alloys’ fatigue strength can be improved by undertaking surface treatments, shot peening, and using reinforcement materials. This results in considerable resistance improvement of aluminum alloys to fatigue crack initiation and propagation enhancing fatigue strength.
Fracture Toughness of Aluminum Alloy
Fracture toughness illustrates a material’s tendency to resist crack propagation and fracture under stress. When dealing with aluminum alloys, its elemental constitution influences fracture toughness is influenced alongside manufacturing process and environmental conditions.
Generally, aluminum alloys have good fracture toughness due to their high strength-to-weight ratio and good ductility. 7075-T6 aluminum alloy has a fracture toughness of approximately 44 MPa·m^(1/2) in plane strain conditions.
Rockwell Hardness of Aluminum Alloy
When describing a material’s Rockwell hardness, you measure its resistance to indentation or penetration by a hard object. The Rockwell hardness of aluminum alloys can vary depending on the specific alloy and its processing history.
Aluminum alloys typically have relatively low Rockwell hardness values due to their low density and high ductility ranging from B40 to B100. The aluminum alloy 6061-T6 has a Rockwell hardness value of approximately B60 while for 7075-T6 it’s slightly higher at about B80.
A summary of aluminum alloys mechanical properties is tabulated as follows:
Aluminum Alloy Series | Tensile Strength (Ultimate) | Poisson’s Ratio | Fatigue Strength | Brinell Hardness | Modulus of Elasticity |
1000 Series | 45.0 – 205 MPa | 0.330 | 20.7 – 62.1 MPa | 12.0 – 55.0 | 62.0 – 69.0 GPa |
2000 Series | 172 – 670 MPa | 0.300 – 0.340 | 80.0 – 469 MPa | 45.0 – 150 | 70.0 – 117 GPa |
3000 Series | 90.0 – 295 MPa | 0.330 – 0.350 | 48.3 – 110 MPa | 28.0 – 79.0 | 68.9 – 71.0 GPa |
4000 Series | 110 – 427 MPa | 0.340 | 45.0 – 393 MPa | 39.0 – 140 | 77.0 – 90.0 GPa |
5000 Series | 110 – 590 MPa | 0.330 – 0.360 | 82.7 – 365 MPa | 28.0 – 185 | 68.9 – 73.0 GPa |
6000 Series | 89.6 – 565 MPa | 0.296 – 0.330 | 55.0 – 517 MPa | 25.0 – 130 | 67.0 – 140 GPa |
7000 Series | 70.0 – 750 MPa | 0.330 | 140 – 425 MPa | 20.0 – 210 | 67.0 – 73.0 GPa |
8000 Series | 70 MPa | _ | _ | 145 – 180 | 71.0 GPa |
Thermal Properties
Aluminum Alloy Melting and Boling Points
The melting and boiling points of aluminum alloys vary with elemental composition with relatively lower melting and boiling points than other metals. Pure aluminum melts at about 660 oC and boils at approximately 2,470 oC, however these figures change when in alloy form.
You find the melting and boiling points can increase or reduce depending on the primary alloying element used alongside aluminum. For instance the alloy 6061 has a melting point of 580 oC and a boiling point around 2,671 oC.

Aluminum Alloys Maximum Working Temperature
The maximum working temperature of an aluminum alloy will depend on its constituent elements and intended application. Factors influencing the maximum working temperature of an aluminum alloy include, its melting point, oxidation, creep and its thermal expansion rate.
Aluminum alloys can be used to temperatures of around 250-300 oC for short time intervals. Where you have longer periods, the maximum working temperature may be lower.
Aluminum Alloy CTE
The coefficient of thermal expansion (CTE) measures a material’s extent of change in size in response to changes in temperature. While aluminum alloys have a relatively high CTE compared to other metals, it varies depending on its structure.
The CTE of aluminum alloys typically ranges from around 21 to 24 x 10-6 oC depending on the alloy structure. This means that when the temperature increases by a single degree, the material expands by 21 to 24 ppm.
Aluminum Alloy Thermal Conductivity
Aluminum alloy structure contributes to superior thermal properties.
The thermal conductivity of aluminum alloys ranges from around 100 to 240 W/(m-K) making them suitable for applications requiring efficient heat transfer.
It is noteworthy that thermal conductivity of aluminum alloys is influenced by external factors like temperature, pressure, and surface condition.
High Temperature Resistant Aluminum Alloy
Aluminum alloys employing copper as the primary alloying element such as 2618-T61 display the highest temperature resistance.
The maximum working temperature of an aluminum alloy influences its temperature resistance. Most aluminum alloys have a maximum working temperature ranging between 250-300 oC.
The following is a summary of aluminum alloys’ thermal properties:
Aluminum Alloy Series | Melting Point | Thermal Conductivity | CTE |
1000 Series | 643 – 660 °C | 218 – 243 W/m-K | 21.8 – 25.5 µm/m-°C |
2000 Series | 502 – 670 °C | 84.0 – 200 W/m-K | 16.0 – 25.6 µm/m-°C |
3000 Series | 629 – 655 °C | 154 – 193 W/m-K | 21.5 – 25.5 µm/m-°C |
4000 Series | 532 – 632 °C | 120 – 180 W/m-K | 17.3 – 23.7 µm/m-°C |
5000 Series | 568 – 657 °C | 105 – 205 W/m-K | 21.8 – 26.1 µm/m-°C |
6000 Series | 554 – 655 °C | 130 – 226 W/m-K | 12.1 – 25.6 µm/m-°C |
7000 Series | 476 – 657 °C | 115 – 222 W/m-K | 21.4 – 25.5 µm/m-°C |
8000 Series | 645.0 – 655.0 °C | 190-210 W/mK | _ |
Electrical Properties
Aluminum Electrical Conductivity
Aluminum alloys have decent electrical conductivity, making them ideal for electrical applications with conductivity determined by its structure. Adding elements such as copper, magnesium, silicon, and zinc to aluminum during the alloying process greatly influences electrical conductivity.
They uilize large alloying amounts of copper offer higher electrical conductivity albeit at lower corrosion resistance. Contrarily, adding magnesium to aluminum during alloying lowers electrical conductivity.
The electrical conductivity of aluminum alloys amounts to about 35 to 60% of pure copper’s capability. A good example is the Aluminum 8000 alloy. It exhibits high thermal conductivity.
More Resources:
- Aluminum Element – Source: RSC
- Aluminum Properties – Source: Sciencing
Types of Aluminum Alloys
Wrought Aluminum Alloys
Aluminum alloy grade is basically a composition of containing Aluminum with other elements. Usually, the alloying process involves:
- Melting aluminum
- Incorporate alloying elements
- Removing impurities
- Mixing to form homogenous solution
- Cooling or extruding to form billets, sheets, tubes, etc.
The quantity of alloying elements in Alu is about 15%.
Aluminum Alloys have special designations set aside for easy identification.
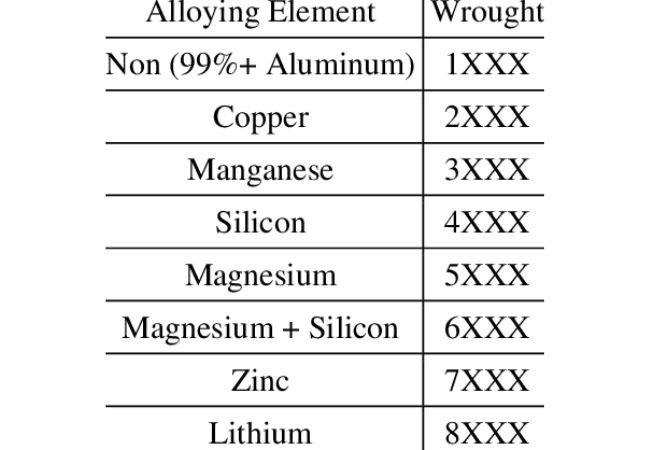
Aluminum Classification
Usually, aluminum classification depends on the chemical composition. These include such properties as their response to mechanical and thermal treatment.
Furthermore, the main alloying element also plays an integral role in grouping aluminum alloys. We can break down Aluminum into three main categories.
These are:
- Casting alloys
- Wrought
- Non-wrought heat treatable alloys.
The general composition of wrought non-heat treatable alloys high purity aluminum alloys.
They aluminum alloys belong to:
- 1xxx
- 3xxx
- 5xxx
This means that you can only harden them by mainly cold working.
The main alloying elements in wrought heat treatable alloys are:
- Zinc
- Magnesium
- Copper
Such alloys can easily be hardened by precipitation.
Aluminum alloys for casting have a combination of heat-treatable and non-heat-treatable components. Common series are:
- 2xxx
- 3xxx
- 4xxx
- 7xxx
- 8xxx
Usually, these Alu series alloy contain a common name but differentiated with varying four digit numbers in series.

Common aluminum alloy series:
Aluminum Series 1000
When it comes to this series, its generally considered as a soft alloy. This Series is commercially pure because it contains Aluminum at over 99% composition.
Their thermal and electrical conductivities are excellent with additional resistance to corrosion. You can efficiently use them in processes requiring extreme deformation.
You can also apply hot forming as easily as cold working on this series. Unlike other series, you cannot use heat treatment to harden them.

Advantages Off Alloy 1000 Series
i. They are the most suitable in applications having extreme deformation
ii. In as much you can weld them, they melting range is very slim
Limitations of Alloy 1000 Series
i. They are very ductile and relatively soft
ii. Compared to other series, their mechanical properties are very poor
iii. Its tensile strength and yield are extremely low
Grades Of Alloy 1000 Series
Alloy Series | Description |
1060 | · This Aluminum alloy grade is commercially pure · Forming process is through rolling and extrusion · High corrosion resistance · Has poor mechanical properties · Strengthened using cold working · Applications mostly in the chemical and electrical industries |
1070 | · Its corrosion resistance is high for a wrought alloy · Its brazing ability is exceptional · Used in making building and construction materials · Also used in making communication cables and other electrical materials |
1100 | · This Aluminum is commercially pure and low cost · It has a narrow melting range · Very ductile and can be easily welded · Used in the manufacture of equipment used in high purity chemical processes · Can also be used to make nameplates, fin stocks and fan blades · Used in electrical works for heat insulators and lighting |
· | |
1350 | · Majorly used in making electrical conductors |
More resources:
- Types of Aluminum – Source: Thomas Net
- Aluminum Grades – Source: Wikipedia
- 1100 Aluminum – Source: Wikipedia
Aluminum Series 2000
The major alloying element used in this series is copper. It also contains traces of magnesium, silicon and manganese.
You can easily boost their strength by heat treating or by precipitation-hardening them. This makes machinability very easy due to the additional hardness.

Advantages Off Alloy 2000 Series
i. Easy machinability therefore providing surface with smoother finishes
ii. They have high thermal conductivity
iii. They are strong and hard with excellent fracture resistance
iv. They can withstand stress and heavy pressure for long
Limitations Of Alloy 2000 Series
i. The presence of intermetallic compounds makes this series difficult to weld. Arc welding them may result in corrosion or hot cracking.
ii. Its corrosion resistance is very low. This means that you need to anodize or coat the alloy during application.
Grades Of Alloy 2000 Series
Alloy Series | Description |
2011 | · They are majorly used to make screws in machine products · They are also used to make fasteners in the electronic and automotive industries |
2014 | · Used to make automotive frames in trucks · Can also be used to fabricate machine parts such as engine pistons and cylinders |
2017 | · Used in making machine parts · Can also be used in manufacturing parts used in screwing machines and fasteners |
2024 | · Usually used in building applications that require high strength materials · Its workability and machinability are fairly excellent · Can be used to make structural aircraft parts and truck wheels. · Can also be used to manufacture gears for machines and other automotive parts |
2219 | · Mostly used to make structures used at very high temperatures of about 315°C. · Its weldments are also high strength |
More resources:
- Understanding Alu Alloys – Source: AlcoTec
- Aluminum 2218 Grade – Source: Wikipedia
- Aluminum Grade 2xxx series – Source: AZO Material
Aluminum Series 3000
It has manganese, which forms the main alloying element.
Its composition ranges between 0.05 to 1.5% of the total alloy mass.

Manganese contributes to the Alu alloy superior mechanical strength. For hardening, choose cold working and not heat treatment.
Advantages Off Alloy 3000 Series
i. It has a very high mechanical strength
ii. Its thermal conductivity is quite good
iii. The alloy has a high tensile strength
iv. It can be welded easily in addition to being brazed and spun
v. Resistant to corrosion
Limitations Of Alloy 3000 Series
i. They cannot be heat-treated
Grades Of Alloy 3000 Series
Alloy Series | Description and applications |
3003 | · It is the most widely-known alloy used for general purposes · Its formability and weldability are similar to those of 1100 although this 3003 is much stronger · Its general applications include making of storage tanks, utensils and appliance parts. · They are also used in sheet metal works in addition to architectural, agricultural and electronic applications |
3004 | · It cannot be heat-treated · Applied in sheet metal works, making of recreational vehicle bodies, trailers and trucks · Additionally, they are used in making kitchenware and building products |
3105 | · It is slightly stronger than the 3003 grade · Used in making equipment used in hospitals for medical purposes · Other applications are sheet metal works, making of kitchen equipment and electronics and building products · Building applications that are not critical like roofing and side ducts |
More resources:
- Aluminum 3003 Grade – Source: KDM
- Aluminum Grade 3xxx Series –AZO Material
Aluminum Series 4000
The major element used in alloying this series is Silicon. The Silicon mass composition is around 3 to 13% of the total alloy mass.
It may also contain small traces of Magnesium and Copper.

Advantages Off Alloy 4000 Series
i. It has a very low melting point
ii. Its fluidity in molten state is greatly improved
iii. Can be easily welded
iv. Heat treatable
v. Good machinability
Limitations Of Alloy 4000 Series
i. Its coefficient of thermal expansion is low
Applications
During the process of welding, it can be used as a filler material. Its thermal properties also make it suitable for making brazing and welding wires together with forged engine pistons.
Grades Of Alloy 4000 Series
Alloy Series | Description |
4032 | · Has very good workability · Has a very high tensile strength · Used to manufacture engine pistons and parts operating in high temperature places |
4043 | · Its color is naturally gray · Its solidification shrinkage is very low · Used mostly in anodizing applications |
4145 | · Has a very high thermal conductivity · It has very good fluidity · Mostly used as thermal treatments after welding has been carried out |
More resources:
- Aluminum Silicone Alloy -Source: Science Direct
- Aluminum Specification & Classification – Source: AZO Materials
Aluminum Series 5000
The major alloying element in this series is Magnesium with a 0.5 to 5.5% of total alloy composition. Magnesium is also found in very small quantities in some of the grades in this alloy series.
Heat-treating this alloy is not possible therefore hardening can only be done by cold-working.

Advantages Off Alloy 5000 Series
i. When annealed, their ductility is very high
ii. They are very easily welded
iii. They have a high resistance to corrosion
iv. The alloy has a high material strength
v. Some grades have excellent workability
Limitations Of Alloy 5000 Series
i. Some grades containing traces of Magnesium cannot be used in high temperature uses. They are very vulnerable to stress corrosion cracking
ii. They cannot be heat-treated
Grades Of Alloy 5000 Series
Alloy Series | Description |
5005 | · Used specifically for instances where anodizing has to be carried out · Compared to 3003, the coating in this grade has a lighter color and is very clean · Used to make equipment that require an excellent electrical conductivity as well as automotive parts. · Its uses can also be found in the marine industry in addition to making kitchen and medical equipment. |
5052 | · In as much as it has more material strength than 3003, it can form readily. · It can be welded easily and is highly resistant to corrosion · Mostly used in the fabrication of electronic chassis and panels, chemical and kitchen equipment · Parts requiring sheet metal of medium strength can also be made using this grade. · Other applications include making of pressure vessels, marine equipment, road signs and in the architectural and agricultural industries. |
5056 | · Used in making industrial cable sheaths and rivets used in fastening magnesium products · Its applications can also be found in the automotive industry and in making screen wires and zippers |
5083 | · Superior corrosion resistance · Due to its high thermal conductivity, it is recommended for assemblies that have been welded · They include tanks and marine equipment that need full joint strength · It is also used to make low temperature pressure vessels with a good weld efficiency. · Additional applications include making freight cars, TV tower installations, components used to make missiles and other cryogenic applications |
5086 | · Used in applications where emphasis is put on stress corrosion resistance or atmospheric corrosion resistance · They include tanks and marine equipment that need full joint strength · It is also used to make low temperature pressure vessels with a good weld efficiency. · Additional applications include making freight cars, TV tower installations, components used to make missiles and other cryogenic applications · Basically the same as 5083 but with emphasis on stress and atmospheric corrosion resistance |
5454 | · Majorly used in the manufacture of any type of welded assembly. · Also used to manufactures vessels and pressure tanks · Trucks used in pouring hot asphalt on roads and dump bodies are also made from this alloy grade · Storages used for hydrogen peroxide and other chemicals are also made of 5454 |
5456 | · Mainly used in the manufacture of any type of welded assembly. · Also used to manufactures vessels, pressure tanks and marine equipment · Applications where excellent weld efficiency is a requirement · Its applications are restricted to environments where temperatures do not exceed 65°C |
5657 | · Used in automotive parts that require anodizing and in making name plates |
More resources:
- Aluminum 5754 Alloy – Source: KDM
- Aluminum Grade 5xxx Series – Source: AZO Material
Aluminum Grade 6000 Series
They have both magnesium and silicone. Magnesium is around 1.5% while Silicon is approximately 1.8% of the total alloy composition.
You can increase yield strength through heat treatment. Furthermore, precipitation hardening is made possible by the high contents of silicon.

Advantages Off Alloy 6000 Series
i. They have impeccable formability
ii. They are corrosion resistant
iii. Easy machinability
iv. High mechanical strength
Limitations Of Alloy 6000 Series
- They are not easily welded. This is because they are very sensitive to solidification cracking.
Grades Of Alloy 6000 Series
Alloy Series | Description |
6061 | · Excellent corrosion resistance · It has an excellent surface quality with an exceptional strength-to-weight ratio · It is a general-purpose alloy with varied applications in industries such as automotive, marine, electronic and agricultural. · It can also be used to manufacture aircraft parts, kitchen and medical equipment, storage tanks as well as recreational vehicle parts. · Other welded and structural assembly applications are fan blades, rail road cars and building products. · Superior strength |
6063 | · It is good for anodizing since the melting point has been reduced by silicon and strength boosted by magnesium. · Can be used in the manufacture of rail piping and architectural extrusions among other building products · Apart from electronic and electrical parts, they are also used in making road signs and kitchen and medical equipment · Others are trailers and trucks including recreational vehicle, appliance parts and marine equipment |
More resources:
- 6061 vs 6063 Aluminum Grade – Source: KDM
- 6000 Series Alu – Source: Science Direct
Aluminum Series 7000
The Series 7000 has its main alloying element as Zinc having a composition range of 0.8 to 8.2%. They are high strength alloy of aluminum.
Heat-treating is the main way in which the strength of these alloys is reinforced. However, you have to follow it with aging to attain a higher yield strength.
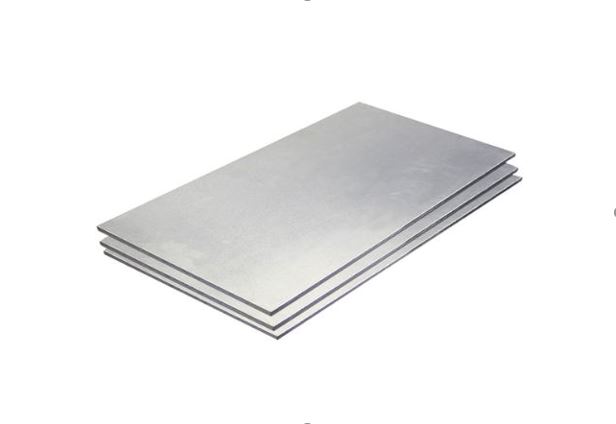
Advantages Off Alloy 7000 Series
i. It is highly resistant to corrosion. This can further be increased by adding copper to the alloy
ii. Grades in this series have high mechanical strength
iii. They can be welded by using either fuse or spot method
Limitations Of Alloy 7000 Series
i. Due to their susceptibility to hot cracking, they cannot be easily welded
Grades Of Alloy 7000 Series
Alloy Series | Description |
7050 | · It’s an alloy grade with a very high strength · Used mainly in making very strong aircraft parts · It can also be used in making ordinance and various equipment used for recreation |
7075 | · Highly resistant to corrosion · Used in making very strong aircraft parts · It can also be used in making ordinance and various equipment used for recreation |
More resources:
- 7000 Series Aluminum – Source: Science Direct
- Aluminum 7029 Alloy -Source: AZO Material
Aluminum Series 8000
The main element used to alloy Aluminum in this series is Lithium. The density of Lithium is lower than Aluminum with a very high solubility.
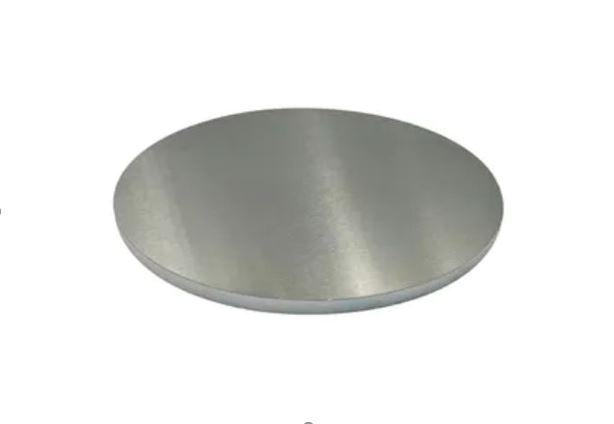
This means that the density of this alloy grade has been reduced with its stiffness enhanced. They are generally strong and tough.
Grades Of Alloy 8000 Series
Alloy Series | Description |
8011 | · Used in manufacture of bottle caps · In Aluminum alloy foil form, it used in car radiators |
8030 | · Its welding capabilities and machining are exceptional · Very strong and light weight · Has very high heat and corrosion resistance · Mainly used in manufacturing electrical conductors · They can also make aircraft and automotive parts |
8090 | · Used in the construction of aerospace material containing very advanced technology · Its light weight is utilized in reducing army ordinance equipment weight and the weight of other defense systems |
8176 | · It is ductile and non-magnetic · It cannot be heat treated · Used in the manufacture of electrical service cables and building wires |
More resources:
- 8000 Series Aluminum – Source: ASTM
- Aluminum 8006 Grade – Source: AZO Material
1. Cast Aluminum Alloys
Casting remains the primary process for making these aluminum alloy. Some major benefits derived from cast aluminum alloys are high strength-to-weight ratio, excellent corrosion resistance, and fine structure.
Examples of cast aluminum alloys are:
i. Al-Si alloys: Silicone dominates the cast aluminum alloy. They are known for exceptional strength, lightweight and wear resistance.
ii. Al-Cu alloys: Utilize copper as the primary alloying element displaying high strength and good machinability and commonly applied in marine and aircraft applications.
iii. Al-Zn alloys: Zinc is the main alloying element offering high strength and good castability and employed automotive parts manufacture.
iv. Al-Mg alloys: Combining copper with magnesium improves corrosion resistance and weldability allowing marine application such as making boat hulls.
v. Al-Ti alloys: Titanium offers enhanced strength and creep resistance to the aluminum alloy mostly applied in aerospace applications.
Heat-Treatable Aluminum Alloys
Through thermal treatments, aluminum alloys acquire better mechanical strength.
Heat treating an aluminum alloy involves raising the temperature of the alloy to a specific value for a sustained period before cooling it rapidly.
These alloys can be subjected to different temper options resulting in different mechanical properties.
Temper options are highlighted by the letter T followed by a digit(s) usually from 1 through 10. The configuration indicates specific sequences of treatments as follows:
- T1: Undertaken through a naturally aging process until stability is achieved especially where high temperature and rapid cooling is utilized.
- T2: Specific to cast aluminum alloys subjected through annealing enhancing ductility and dimensional stability.
- T3: The molten alloy material is subjected to heat treatment before cold working and a natural aging process until stability is achieved.
- T4: Encompasses a heat treatment and natural aging process of the molten alloy material to a specific temperature. It is thereafter quenched in a cooling medium, aging under natural conditions at room temperature resulting in medium strength and good formability.
- T5: Employs only artificial aging following a high temperature fabrication process followed by rapid cooling augmenting strength and dimensional stability.
- T6: Utilizes a heat treatment followed by artificial aging for the molten alloy material by heating at reduced temperature. Results in high strength and toughness.
- T7: An over aging process follows the heat treatment of the molten alloying material. The result is enhanced toughness and corrosion resistance but reduced strength.
- T8: After heat treating the molten alloy material, it is cold worked before aging artificially enhancing strength performance.
- T9: The sequence with this temper option is a heat treatment process, followed by artificial aging before finally cold working.
- T10: Incorporates artificial aging and cold working following a fabrication process at high temperatures and rapid cooling.
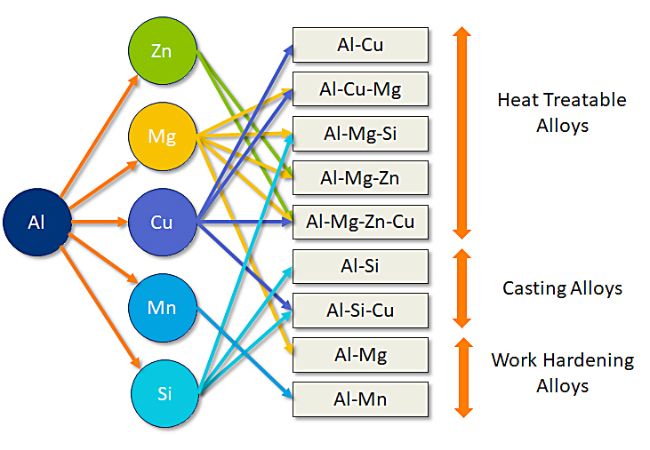
Non-Heat Treatable Aluminum Alloys
Non-heat treatable aluminum alloys cannot be strengthened by employing heat treatment finding use where corrosion resistance and formability are pivotal. Such alloys are strengthened though alternative means like strain hardening and cold working via processes like drawing and rolling.
Non-heat treatable aluminum alloys include:
a. 1XXX Series: Employ pure aluminum making them the softest and most ductile finding use as electrical conductors and in cooking utensils.
b. 3XXX Series: Contain manganese as the primary alloying element. They are valued, especially in the automotive industry, for their formability, weldability, and corrosion resistance.
c. 4XXX Series: Utilize silicon as the main element when alloying with aluminum exhibiting good weldability, wear resistance and fluidity. These aluminum alloys find use in welding operations as filler material, architectural applications and making engine parts.
d. 5XXX Series: These non-heat treatable alloys are made up of magnesium and exhibit high strength and enhanced weldability and corrosion resistance. They are perfect choice for most roofing materials.

Weldable Aluminum Alloys
Weldable aluminum alloys are capable of being joined by applying heat such that the mating parts melt and cool together. Welding aluminum possess a challenge stemming from its thermal conductivity and disposition to form an oxide layer.
Some aluminum alloys that are difficult to weld are:
- 2xxx
- 6xxx
- 7xxx
At the same times, there are aluminum grade alloys you can use as filler material during welding such as the 4xxx.
Additionally, you can easily weld the 1xxx, 3xxx and 5xxx. Popular options in today’s industries include.
a. 3003: Displays excellent formability allowing use in sheet metal work creating utensils, fuel tanks and electronic bodies.
b. 5052-H32: Exhibits impressive weldability and resistance to corrosion finding use in marine applications, making tanks and pressure vessels.
c. 5083-H321: Demonstrates high efficacy in welding resulting in strong joints with excellent resistance to corrosion. Consequently, they find use in harsh environments like marine and industrial applications.
d. 5054: These alloys have excellent weldability and strength performance and are utilized used in high heat applications and storage vessels.
e. 5086-H32: This weldable aluminum alloy offers high strength too and common in structural applications such as boat building and making truck bodies.
f. 6061-T6: Its good weldability and high strength allows use in structural applications such as bridges, railroads, buildings, automotive and aircraft components.
g. 6063-T6: Offers good weldability, corrosion resistance and medium strength commonly advantaged in architectural applications making window and door frames.

Alloyed Aluminum Manufacturing Process
Aluminum is one of the most concentrated elements on earth that finds wide usage across industries. While it doesn’t occur naturally in its pure form, it is extracted from mineral ores usually in combination with other elements.
Step 1: Extracting Aluminum from Ore
Aluminum is typically extracted for commercial use from the mineral ore bauxite. Bauxite is often found near the surface of the earth and extracted through open-pit mining.
The bauxite ore is thereafter transferred to a plant where pure alumina is extracted via the Bayer process as follows:
Refining
The bauxite ore is first refined to eliminate impurities and excess materials, such as silica, iron, and titanium. Here, it is crushed and grinded to a fine powder and compounded with sodium hydroxide at high temperatures and pressures.
This results in the production of a slurry solution referred to as sodium aluminate and red mud containing unwanted mineral elements. The red mud typically sinks from where it is eliminated and the slurry further filtered to eliminate any remaining red mud.
Precipitation
The resulting sodium aluminate solution is subjected to carbon dioxide treatment to precipitate aluminum hydroxide. The aluminum hydroxide is then washed before drying and heating in a kiln to produce alumina in a calcination process.
Reduction
The alumina is mixed with cryolite which lowers the melting point of the alumina and subjected to a large electric current. This is the Hall-Héroult process and results in the reduction of molten by removing oxygen leaving behind pure molten aluminum. .
Step 2: Adding Alloying Elements to Aluminum
Aluminum can also be recycled greatly saving costs since when compared to extraction from bauxite, it costs only about five percent. Alloying elements are added to molten aluminum in the desired proportions before being transformed into ingots.
Step 3: Converting Aluminum Alloy to Useful Products
Aluminum alloys offer improved physical and mechanical properties to pure aluminum. These include strength, corrosion resistance and hardness allowing for wider application.
Here is how you can prepare aluminum alloy ingots:
Extrusion
Allows you to obtain a profile with a fixed cross-section by forcing the molten aluminum alloy through a specially-shaped die. It is thereafter taken through stress relief by cooling and stretching.
Rolling
After casting the aluminum alloy into beams of appropriate dimensions, it is rolled into sheets. Large rollers subject the beam into a compression force flattening it into the desired depth size.
Casting
Here, molten aluminum alloy is cast into a die with the appropriate mold shape where it is cooled and solidified. Casting allows processing of aluminum alloy into complex shapes.
Alloy Aluminum Sheet
The process of making aluminum sheets begins with the melting of ingots of aluminum alloys before casting into slabs. The slab parameters determine the thickness of the aluminum alloy sheet achieved through rolling.
The rolling process utilizes a series of rollers gradually reducing the thickness of the aluminum alloy slab by applying pressure. After achieving the desired thickness, it is subjected to annealing to improve its strength and ductility.
Aluminum Alloy Rods
Aluminum alloy rods are utilized in the construction, automotive, and aerospace industries where the grade selected depends on the desired properties. In making aluminum alloy rods, the casting method is used to form large bars similar to the desired rod size.
The bars are then extruded through a die shaped in the size of the rod in a hot working procedure. This reduces the cross-section of the bar elongating it. You can require successive dies to achieve the desired dimensions after which you can cut to desired length.
Aluminum Alloy Coil
Aluminum alloy coils are made by a combination of processes including casting, rolling and slitting. After rolling cast aluminum alloy billets into the desired thickness, they are slit into narrow strips to the desired width.
A drawing process can be conducted to convert the strips into different shapes before winding over a spool to create a coil. The resulting coil can also be subjected to compression forces when making components like springs.
Aluminum Alloy Pipe
Aluminum alloy is typically converted into pipes via extrusion where it is forced through a die to obtain a continuous profile. The die determines the parameters of the pipe and is usually fashioned from high-strength material.
You can have successive dies with different sizes or shapes to achieve the desired end result. After extruding the pipe, you cool it, cut it to the desired length and when necessary undertake further processing.
Aluminum Alloy Bars
Making aluminum alloy bars also employs extrusion utilizing a die system in the desired bar profile. It is a hot working process to allow easy shaping of the aluminum alloy into a bar. The extrusion process is succeeded by a cooling process after which the bars are cut into desired lengths.
Aluminum Alloy Cylinder
Like in aluminum alloy bar and pipe making, extrusion is utilized in producing aluminum alloy cylinders. Extrusion allows you to produce cylinders in different sizes and shapes by using different die design according to the specifications.
Step 4: Heat Treatment for Alloy Aluminum
Using heat treatment processes on aluminum alloy helps you to improve its mechanical properties. The choice of heat treatment process depends on the type of aluminum alloy, the desired properties, and the intended application.
Some common heat treatment processes for aluminum alloys are discussed below:
Annealing
Improves ductility and involves heating the aluminum alloy to a specific temperature before gradually cooling. Annealing makes shaping the aluminum alloy easier when conducting further processing.
Precipitation Hardening
This heat treatment process augments the strength and hardness of the aluminum alloy. After solution heat treatment, aging is done at low temperature.
This results in the formation of hard particles within the aluminum matrix by the dissolved elements.
Quenching
When quenching aluminum alloy, you rapidly cool it to room temperature from a high temperature. The end result is a microstructure that exhibits great strength and wear resistance.
Solution Heat Treatment
In this heat treatment process, you heat the alloy to a temperature exceeding the alloying elements’ solvus temperature. The alloying elements dissolve in the matrix forming a homogeneous mix that you quench trapping the elements in the matrix.
Tempering
Tempering is a secondary heating process you execute on the aluminum alloy already quenched or hardened to a lower temperature. The result is an improvement in the alloy toughness and a reduction in its hardness and brittleness.
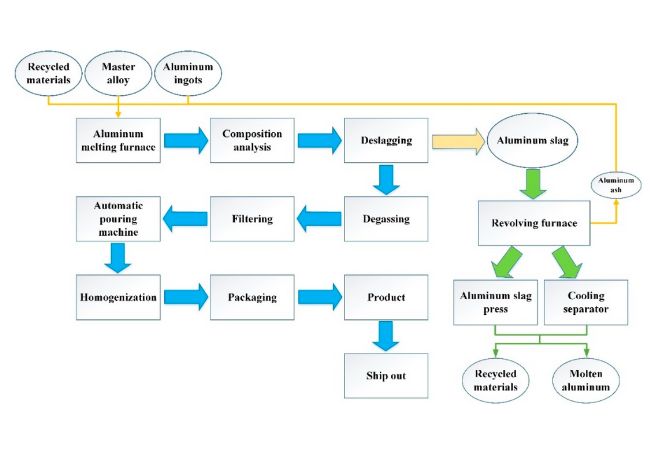
Step 5: Fabricating and Machining Aluminum Alloys
There are several fabricating and machining processes performed on aluminum alloys to convert them into useful products.
Some of these processes include:
Laser Cutting
Laser cutting utilizes a high-powered laser beam to melt and vaporize material from a workpiece. Using laser cutting on aluminum alloys is versatile and efficient, however requires careful consideration to successfully achieve high-quality results.
Aluminum alloys are highly reflective making laser cutting a challenge since it can reflect the beam hampering the cutting process. The beam can damage the laser equipment while its reflection or scattering can result in poor cut quality and/or reduced cutting speed.
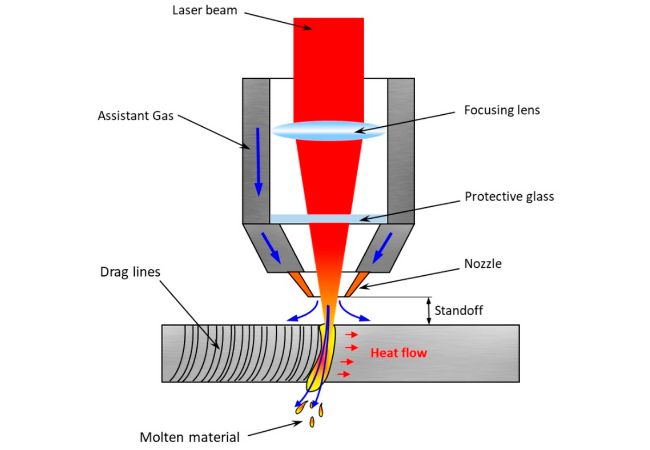
You can address this challenge by utilizing a wavelength capable of absorption by the aluminum alloys like fiber lasers. Addressing burr formation is also necessary by using assisted gas pressure and adjusting the cutting parameters like speed of cutting and power.
Bending Aluminum Alloy
Bending allows you to create curved or angular shapes of aluminum alloys for various applications like aerospace and automotive. However, the low ductility of aluminum alloys and tendency to spring back makes bending these alloys challenging.
Dissimilar ductility in aluminum alloy is due to their varying alloying elements. Consequently, they determine either breaking or cracking during aluminum bending process.
Another factor to consider when bending aluminum alloys is thickness where the tendency to crack increases with increase in thickness.
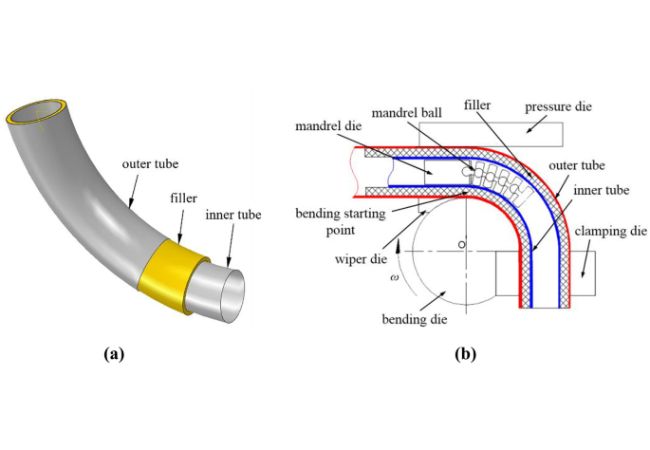
It is important to use a lubricant during the bending process to reduce friction and prevent cracking. Carefully controlling the bending process like the bending parameters of force, radius and angle is useful in regulating spring back.
Drilling Aluminum Alloy
Drilling allows you to create holes in aluminum alloys for design purposes such as joining parts and fulfilling aesthetic considerations. When drilling aluminum alloys, it is advisable to use a high-speed steel (HSS) or cobalt drill since they’re durable and temperature tolerant.
Use a high drilling speed and low feed rate to prevent a poor-quality outcome since aluminum alloys are relatively soft. Note that a sharply edged drill bit with an obtuse point angle can ensure a clean and precise outcome.
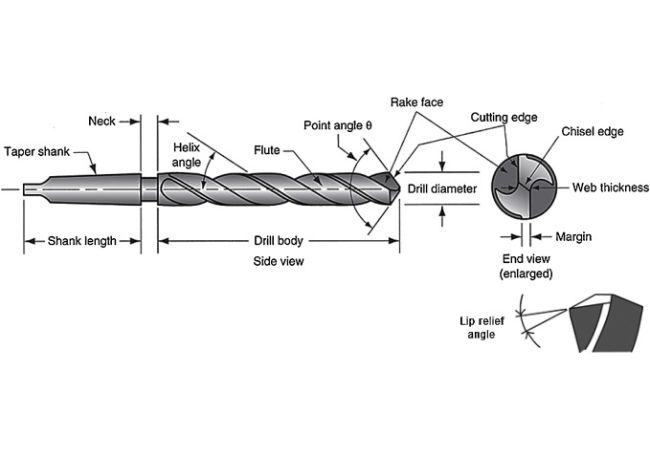
Drilling aluminum alloys is also affected by the thickness of the material. For instance, for thicker materials, slower drilling speeds and higher feed rates are necessary to avoid overheating or excessive bit wear.
Aluminum Alloy Machining
Machining processes on aluminum alloys entail removal of material to achieve a desired outcome. In undertaking machining operations on aluminium alloy, consider the cutting tool ensuring they’re durable and tolerant to high temperatures.
Since alloys constitute different elements, they have varying levels of machinability requiring individual consideration before machining. This ultimately affects parameters such as feed rate and machining speed to ensure the resulting work is of quality.
Aluminum alloys containing copper as the primary alloying element are highly machinable compared to those containing silicon or zinc. Carbide cutting tools offer better performance when used in machining aluminum alloys.
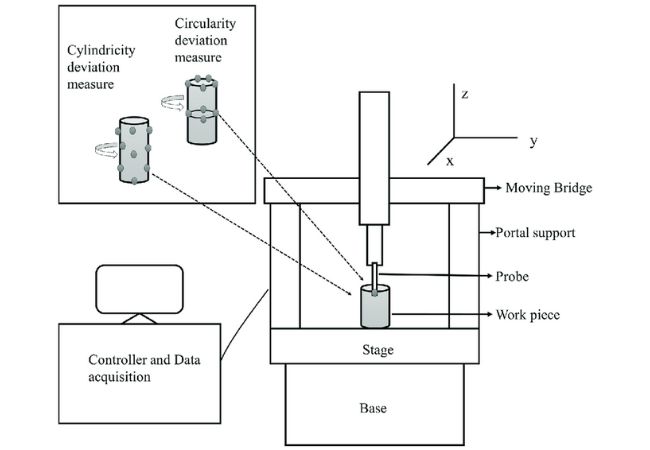
Aluminum Alloy Extrusion
Extrusion allows you to create complex aluminum alloy shapes and profiles by forcing it through a die after heating. The differing properties of aluminum alloys based on their constitution affects their ability to be extruded without cracking or breaking.
The temperature at which extrusion is carried out is influenced by the alloy composition and so is the extruding force. A die system determines the shape and complexity of the extruded aluminum alloy profile.

Die Casting Aluminum Alloys
When producing high-volume, complex-shaped aluminum alloy components, molten metal is injected into a mold cavity (die) via a die casting process. The aluminum alloy is delivered into the die under pressure thanks to a press system.
A pattern in the desired shape of the aluminum alloy makes the die which then takes the negative image. The molten alloy upon filling the die cavity is left to solidify before being broken out or ejected off the die.
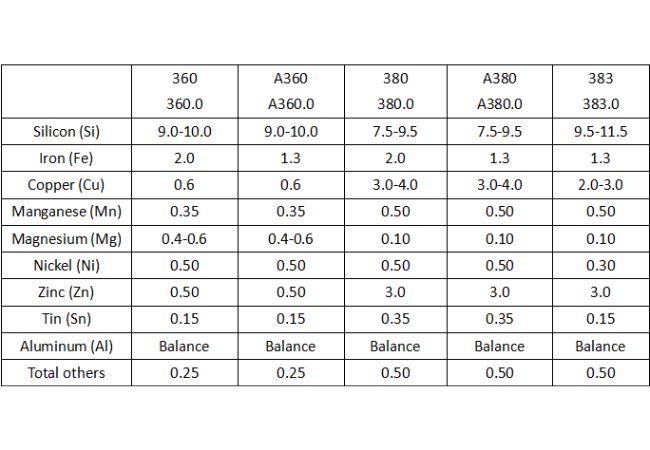
Drawing Aluminum Alloy
Drawing allows you to produce long, thin, and cylindrical aluminum alloy parts such as wires, tubes, and bars. You pull the aluminum alloy through a series of dies with progressively smaller diameters resulting in a longer and smaller profile.
Heating the aluminum alloy before drawing allows for easier workability when pulling it through the dies in the desired profile. The temperature to which you treat the aluminum alloy before drawing depends on the constituent elements.

Forged Aluminum Alloy
When forging aluminum alloys, application of compressive forces shape the material beyond its yield strength altering the shape and mechanical properties. Consider the alloying elements’ properties such as strength and ductility to prevent damage during forging such as cracking or even breaking.
It is typical to carry out hot forging with aluminum alloys to improve workability before shaping using a hammer or press. Forging encompasses application of a series of blows that turn the aluminium alloy into the wanted form.
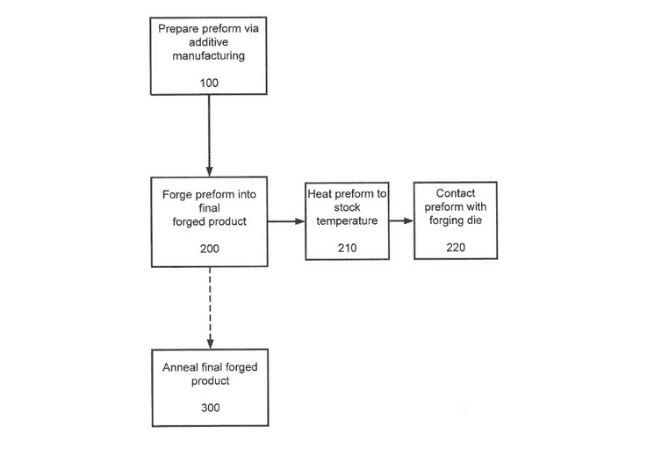
Welding Aluminum Alloy
Welding aluminum alloys allows you to join multiple pieces by melting and fusing them together. However, welding these alloy grades is challenging given their low melting point, high CTE and oxide layer formation.
Not all aluminium alloys are considered weldable, some requiring special maneuvers to successfully execute. Welding methods such as gas tungsten and gas metal arc welding are utilized in welding aluminum alloys.

Most aluminum alloys utilizing silicon as the primary alloying element are used as fillers in welding applications. Contrarily, aluminum-zinc alloys offer weldability as one of the outstanding properties.
Alloyed Aluminum Cutting
Cutting allows you to shape aluminum alloys into specific parts or components utilizing different methods from mechanical, thermal to abrasive cutting. Mechanical methods such as sawing utilize specially shaped and wear resistant blades to allow you cut straight through aluminum alloys.
Plasma cutting utilizes a stream of ionized gas at high-velocity to melt and cut through both thick and thin aluminum alloys. Waterjet cutting contrarily utilizes a stream of high-pressure water mixed with abrasive particles in the cutting process with low heat distortion.
Powder Coating Aluminum Alloy
The application of a dry powder coating to the surface of an aluminum alloy enhances durability and aesthetic appeal. The powder is applied on a clean and contamination free surface usually electrostatically using a spray gun.
A curing process at elevated temperatures follows melting the powder and allowing the coating to transform into a smooth finish. Curing is undertaken in a special heating chamber or an oven while the powder coating can be dyed to enhance appearance.
CNC Machining Aluminum Alloy
Computer Numerical Control (CNC) machining of aluminium alloys allows for the production of complex parts and components. As the name suggest, CNC machining utilizes computer-controlled machines to remove material from an aluminum alloy workpiece.
The CNC machine works by executing the details of a CAD (Computer Aided Design) that is fed to the machine. You can cut complex aluminum parts.
Sand Casting Aluminum Alloys
Sand casting is used in the production of large aluminum alloy parts of complex designs by using sand molds. The mold is fashioned using a pattern in the shape of the aluminum alloy part within which you pour the molten alloy.
The pouring process is controlled to ensure the mold is filled uniformly to prevent defect such as voids. The aluminum alloy is allowed to cool and solidify in the cavity before it is broken out of the mold.
Aluminum Alloy Finishing
Finishing processes on aluminum alloys allow you to improve the surface quality and appearance after a machining or fabrication process. Aluminum alloy finishing encompasses different techniques such as anodizing, brushing, painting, polishing and sandblasting.
Anodizing electrochemically forms a protective oxide layer over the surface of the aluminum alloy improving corrosion and wear resistance. Polishing removes surface imperfections mechanically by utilizing abrasives resulting in a smooth, reflective surface.
More Resources:
- Aluminum Fabrication – Source: KDM
- Aluminum Fabrication – Source: Thomasnet
Aluminum Alloy Maintenance
Cleaning Aluminum Alloys
Cleaning aluminum alloys ensures the surface of the metal is free of contaminants that can affect performance, appearance and durability. Contaminants such as dirt, oils and grease can be removed via the following methods:
i. Acid Cleaning: Entails the use of an acid solution like sulfuric, hydrochloric and phosphoric acid to remove oxide layers and inorganic contaminants.
ii. Electrolytic Cleaning: Eliminates surface contaminants on an aluminum alloy part submerged in an electrolyte solution by subjecting to an electric current.
iii. Mechanical Cleaning: Executed by application of mechanical action such as brushing or blasting effectively removing loose contaminants from the surface.
iv. Solvent Cleaning: Utilizes a special solvent such as acetone, isopropyl alcohol, and trichloroethylene to dissolve and remove surface contaminants like oils and grease.
v. Steam Cleaning: Effective for large scale use, steam cleaning subjects the aluminum alloy parts to a high-pressure steam treatment eliminating contaminants.
Aluminum Grade Alloys Restoration
Aluminum grade alloys can corrode, dull, or get defaced by scratching stemming from continued use and natural wear and tear. Aluminum alloys restoration involves techniques to replenish the metal’s surface finish and eliminate any surface damage.
Some common techniques used in aluminum alloy restoration include:
i. Anodizing: Creates an oxide layer over the aluminum alloy surface by immersing in an electrolytic bath enhancing its resistance to corrosion.
ii. Chemical Cleaning: Utilizes acid or alkaline solutions depending on the corrosion type to remove the surface constraint.
iii. Painting: Involves applying a coating of paint over the surface to offer protection from corrosion usually after cleaning.
iv. Polishing: Uses abrasive materials like sandpaper and buffing tools to eliminate scratches, stains, and surface imperfections resulting in anew shine.
v. Sandblasting: Employs compressed air to blast abrasive materials on the aluminum alloy surface removing surface imperfections
Aluminum Alloy Polishing
Aluminum alloy polishing eliminates surface imperfections like scratches and stains resulting in a smooth, reflective finish. There are different approaches to polishing as follows:
i. Chemical Polishing: Strong chemical solutions dissolves the surface layer of the immersed aluminum alloy leaving a smooth surface that’s is highly reflective.
ii. Electrolytic Polishing: An electric current applied to an electrolytic solution containing the aluminum alloy dissolves the external layer revealing a smooth virgin surface.
iii. High-Pressure Water Jet Polishing: A water jet subjected to high-pressure is concentrated on the surface of the aluminum alloy smoothening it. Abrasive particles can be added to the water jet to increase the surface area of action.
iv. Mechanical Polishing: Utilizes abrasive materials like sand paper to initiate removal of surface imperfections through mechanical action. This can be done manually or using machines resulting in smooth and reflective surface.
v. Vibratory Finishing: The aluminum alloy is enclosed in a container with excited abrasive materials that remove surface imperfections through vibration. The concentration of the particles and speed of particle movements influence the polishing process.
Cost of Alloyed Aluminum
The cost of alloyed aluminum is dependent on different factors prime of which is the elemental constitution. Aluminum alloys combining high value elements like titanium and lithium will cost much higher than say those with zinc or copper.
Additionally, costs vary with the fabrication method utilized for the aluminium alloy. Given the different methods available, investment casting for instance is a costly method that negatively affects cost.
Aluminium alloys will cost you anywhere between $1,400 and $3,500 dollars per ton depending on grade and other factors. These prices fluctuate under the vagaries of the market forces of demand and supply.
Aluminum Alloy Scrap Price
The highly durability of aluminum alloys allows them to be recycled multiple times over without hampering their mechanical qualities. Recycling aluminum also allows large energy savings on production compared to extraction form mineral ores by over ninety percent.
Scrap aluminum alloy is available at different rates across the world with an average price of about $450 per ton. Once scrap aluminum has been processed, it can fetch from $1,400 per ton depending on the market conditions.
Alloying Element Cost and Availability
Aluminum alloys contain different elemental combinations such as copper, magnesium, silicon, zinc, manganese, nickel and iron which determine the alloy grade. These elements each attract different costs depending on their availability and amount required in specific application.
Aluminum alloys cost more than pure aluminum since combining aluminum with other elements requires additional manufacturing processes. Furthermore, the alloying elements require different fabrication processes which affect cost like extrusion and casting.
Geopolitics
Geopolitical factors encompass issues like trade policies, economic conditions, political climate and shifting supply and demand that affect different regions. These factors greatly impact the cost of aluminum alloys due to the sensitivity of the market to changes.
For instance, a change in trade policies affecting say tariffs and embargoes can affect the availability of raw materials for aluminium alloy. Furthermore, when political instability is observed in a major aluminum producing country, chances are the market will be negatively affected.
Demand and Supply
Like other commodities in the international market, aluminum alloys are influenced by the market forces of supply and demand. Consequently, when there’s a high demand for aluminum alloys with limited supply, aluminum alloys prices shoot and the opposite is true.
Supply and demand of aluminum alloys will be affected by various factors such as:
i. Economic growth in countries associated with major aluminum alloy consuming industries can positively influence demand.
ii. Government policies such as passing laws affecting use of aluminum alloys or spearheading import restrictions will affect supply and demand.
iii. Having high rates of recycling of aluminum alloys can increase supply and thus reduce the cost and price of aluminum alloys.
iv. Production levels of aluminum by major producing countries will determine the supply in the market.
v. The cost of alternative materials like steel will affect demand for aluminum alloys in a direct relationship.
How to Quantify Aluminum Alloy Price:
Aluminum Alloy Price Per Pound
Depending on the aluminum alloy grade aluminum prices can start from as low as $0.15 per pound usually for scrap aluminum. However, market conditions can easily push the price to over a dollar for a pound.
Most Expensive Aluminum Alloy
Customized aluminum alloys made for specialized use and not the larger market could be the most expensive in theory. The most expensive aluminum alloys exhibit unique properties and are fashioned from complex production processes and/or utilize high cost raw materials.
The aluminum alloy 7075-T6 which employs zinc as a primary alloying element is presently the most expensive in the market. It is suitable for:
- High stress applications such as aircraft parts
- Known for high strength-to-weight ratio
- Superior fatigue strength
- God yield and tensile strength.
Cheapest Aluminum Alloy
The cheapest aluminum alloy largely consists of pure aluminum with a reduced concentration of alloying elements like the 1100 grade. AA 1100 contains over 99% aluminum content with a very small amount of copper ad an alloying element.
AA 1100 exhibits excellent properties such as formability, weldability, and corrosion resistance. It is utilized in applications like packaging of food and beverage, reflectors for lighting and wide-ranging sheet metal work.
Factors to Consider when Choosing Alloys of Aluminum
When selecting an aluminum alloy for your application, several factors come in mind that should be considered as follows:
- Corrosion Resistance: Aluminum alloys exhibit outstanding corrosion resistance, however, depending on your application you find some alloys offer better corrosion resistance than others.
- Cost: Factors such as the cost of raw materials and production costs influence the overall cost of an aluminum alloy.
- Environmental Considerations: Where there are environmental concerns or issues at play especially at the production and application stage this becomes an important factor.
- Formability: The formability of aluminum alloys depends on the alloying elements, which impacts their ability to be shaped.
- Machinability: Machining is key in furnishing aluminum alloys to the desired form and should therefore be considered when selecting an alloy.
- Strength and Hardness: Aluminum alloys display different levels of strength and hardness based on their elemental composition and treatment.
- Weldability: Some aluminum alloys pose difficulty in welding and should be avoided where welding is intended as a key fabrication process.
International Standard Designations for Aluminum Alloys
There are several international standard designations for aluminum alloys, used to classify aluminum alloys depending on the composition.
These designations are commonly applied in the world:
The Aluminum Association (AA)
This system is accepted worldwide originating providing a four-digit numerical code preceded by the initials AA to identify the aluminum alloy.
Taking the form AA (XXX.X), we have:
- 1st digit – the main alloying element
- 2nd and 3rd digits – different alloys for each series
- 4th – expresses condition of the alloy
Unified Numbering System (UNS)
The unified numbering system utilizes a five-digit code with a prefix letter to identify the material. For instance, aluminum and its alloys are typically contained between A00001 to A99999.
Japanese Industrial Standards (JIS)
JIS designation identifies aluminum alloys in the format JIS H XXXX, where the XXXX is a four digit code for the aluminum alloy.
European Norm (EN)
This designation was put forward by the European Union with two notable formats as follows, where XXXX stands for a digit code:
- EN AW-XXXX (for wrought aluminum alloys) or
- EN AC-XXXX (for cast aluminum alloys).
International Organization for Standardization (ISO)
The ISO format utilizes a prefix indicating the material in this case Al for aluminum, simply followed by the alloy’s chemical composition.
For instance, Al-Mg1SiCu designates an aluminum alloy containing magnesium as the primary alloying element, silicon and copper.
Looking into Future Prospects in Alloyed Aluminum Industry
· New Development and Research on Aluminum Grade Alloy
Efforts are being made worldwide to introduce new aluminum alloys with improved properties and at cheaper costs. Some of these developments include:
Aluminum Combinations With The Following:
a. Lithium
Efforts are underway to combine aluminum with lithium as the primary alloying element to achieve high performance alloys. Utilizing lithium in aluminum alloys has the potential to enhance their strength relative to weight, corrosion resistance, stiffness and fatigue cracking.
b. Scandium
This element seeks to improve weldability of aluminum alloys, improve the tensile strength and reduce cracking during high stress applications. Scandium is however still very costly given its rare occurrence in the ores of other elements.
c. Beryllium
Combining aluminum with beryllium will enhance the strength of the aluminum alloy and also boost its stiffness performance relative to weight.
Furthermore, utilizing beryllium can offer greater stability at high temperatures given its low thermal expansion coefficient. However, beryllium offers the challenge of toxicity to both humans and the environment not to mention its high price.
Additive Manufacturing
New developments are being advanced to utilize aluminum alloys in additive manufacturing like 3D printing. Research is underway to develop aluminum alloys with the necessary qualities like strength, ductility and thermal stability suitable for 3D printing.
Recycling of Aluminum Alloys
Aluminum alloy recycling has been in existence for a while though not at a hundred percent effectiveness. Given the global efforts and concern on matters green, researchers are keen on developing more efficient recycling methods.
The points of concern are to increase the recycling levels worldwide by developing more efficient methods of recycling aluminum alloys. Also, efforts are being made to reduce the environmental impact of aluminum alloy manufacturing and the conservation of natural resources.
Future Applications of Aluminum Alloys
The durability of aluminum alloys has seen their use increase to newer and innovative applications as their properties are further improved. As the world continues to change rapidly with more advanced technology, use of aluminum alloys is destined to increase.
Expect to see aluminum alloys in the following:
Biomedical Implants
Top qualities required for biomedical implants like prosthetic limbs, bone plates, and dentures are biocompatibility and corrosion resistance. Aluminum alloys exhibiting such qualities are being developed to provide a cheaper alternative to titanium implants making them more affordable.
Construction
For years now steel has been the go to metal for construction works thanks to its excellent strength qualities and performance. Aluminum alloys have found limited use in construction with steel still reigning supreme in core aspects like making beams, columns and trusses.
Researchers are intent on developing aluminum alloys with strength performance comparable to steel and capable of replacing it in construction. This will greatly lower construction costs given aluminum alloy’s availability and its recycling capability.
Electric Vehicles
As demand for electric and self-driving vehicles increases, the need to make them even cheaper and affordable arises. Aluminum alloys are an ideal material given their superb mechanical qualities being lightweight and high-strength materials.
Aluminum alloys can be used for making side panels, battery casings, and other structural parts in these vehicles. Furthermore, their capacity to be recycled countless times without affecting their qualities works in their favor.
Renewable Energy
Efforts for a greener planet are now the focus of most governments encouraging the use of renewable energy sources. Alternatives to traditional energy sources such as wind and solar power are being spearheaded necessitating developments.
Given the mechanical properties of aluminum alloys such as corrosion resistance and strength, their use in this industry is apparent. Components for wind turbines like blades, and solar panel frames can be fashioned from aluminum alloys.
Alloy Aluminum Based on Applications
Aluminum Alloys for Aerospace Applications
Aluminum alloys used in aerospace applications are valued for their high strength-to-weight ratio, corrosion resistance, and good thermal conductivity. Common Alu alloys are:
AA 2024
Employs copper as the main alloying element alongside smaller amounts of zinc, magnesium and manganese exhibiting high strength and toughness. It finds common use in making the landing gears, fuselage frames and wing spars of airplanes.
AA 2090
It employs copper alongside lithium and zirconium as alloying elements. It finds use in making bulkhead stiffeners for aircraft floors, fuselage parts and wings thanks to its high strength property.
AA 6061
Utilizes magnesium and silicon as the main elements in the alloying process possessing high strength thanks to precipitation-hardening. It is also weldable and corrosion resistant finding common use in making aircraft wings and fuselages.
AA 6061 is also employed in building boats and making gas cylinders for high pressure storage such as scuba tanks. Some vehicles employ AA 6061 in furnishing their chassis.
AA 7010
With zinc as the primary element 7010 exhibits decent strength qualities with high corrosion tolerance and resistance to damage. It is a wrought aluminum alloy that is utilized in forging components for aerospace use.
AA 7050
Features capable qualities such as toughness, resistance to stress corrosion cracking and strength thanks to zinc and magnesium content. It is heat treatable with relatively high electric conductivity utilized in production of aerospace parts like bulkheads, fuselage frames, and wing skins.
AA 7055
Possesses a high tensile strength over 550 MPa and is a wrought aluminum alloy that is heat treatable. This strength quality allows its use in building aircraft frames.
Examples of parts include aluminum alloy wing skins, aluminum aircraft structure, aluminum fuselage, and other aluminum air craft parts.
Aluminum Alloys for Automotive Applications
Aluminum alloys for automotive applications feature qualities like heat and corrosion resistance as well as high strength. Some aluminum alloys utilized in automotive applications include:
AA 5182
Utilizes magnesium and manganese in the alloying process with aluminum offering high strength to various parts used in the automobile industry.
AA 6013
You find it utilized in modern vehicles making the braking system and engine parts.
AA 7068
Capable of heat treatment with incredible strength qualities like an ultimate tensile strength reaching 700 MPa comparable to some steel types. In the automotive industry, AA 7068 find use in making connecting rod, fuel pumps, and engine valves.
AA 7075
The inclusion of zinc in this alloy gives enhanced mechanical properties such as strength, fatigue resistance, ductility and toughness. It performs considerably well in high stress applications finding use in automotive gears and shafts, and valve parts.
Examples of applications are aluminum alloy wheels, alloy aluminum rims, engine block aluminum alloy, piston aluminum alloy and other aluminum vehicle parts.
Aluminum Alloys for Cryogenic Applications
Cryogenic applications involve very low temperature conditions and as such require aluminum alloys that can retain structural integrity in such cases. Some capable aluminum alloys for use in this case are listed thus:
AA 5059
Combining aluminum and magnesium, it is non-heat hardened instead employing strain hardening or cold working for strengthening. It is weldable and corrosion resistant finding use in cryogenic tanks for propellants used in reusable rockets.
AA 5083
Alongside aluminum and magnesium, this alloy has scant amounts of chromium and manganese with incredible resistance to chemicals and saline water. It is also non-heat treated with relatively high strength parameters not suited for use at over 65 °C.
Consequently, AA 5083 is utilized in cryogenic applications as it can reach up to -195 °C at cooling conditions. This material is noted for increasing its strength parameters when it hits this temperature while displaying superb resistance against fractures.
Examples include aluminum refrigeration equipment.
Aluminum Alloys for Marine Applications
Marine applications emphasize corrosion resistance due to the high interaction of marine structures and vessels with sea water. As such, materials used in these features require to be highly resistant to corrosion to prevent hastened wear.
AA 5052
The structural composition of AA 5052 contains aluminum and magnesium offering improved hardness and resistance to corrosion via cold working processes. This alloy material is mostly applied in marine structures thanks to its tolerance of corrosion inducing saline environments.
AA 5059
Rather than heat hardening, this aluminum-magnesium combination utilizes cold working or strain hardening which greatly improves its strength performance. It is thus weldable without damaging its structure and used to build hulls for marine vessels given they’re also corrosion resistant.
Since heat treatment doesn’t strongly affect the strength, 5059 can be readily welded and retain most of its mechanical strength.
AA 5083
The outstanding property of this alloy material is its resistance to deterioration by chemicals and saline water. It also retains its mechanical formidability after welding allowing use in ship building and construction of off shore rigs.
AA 5086
You can weld this alloy material that is incapable of heat treatment using strain hardening or cold working to improve its strength. Additionally, it’s highly corrosion resistant allowing use in boat building and furnishing gangways for sea vessels.
AA 6061
The primary alloying elements here are magnesium and silicon offering decent mechanical properties such as good weldability and corrosion resistance. They can withstand abrasion allowing use in the construction of boats and yachts.
Examples of applications include aluminum alloy boats, aluminum alloy cable in marine industry, aluminum ship parts, etc.
Aluminum Alloys for Structural Applications
Many structural applications require use of mechanically durable materials especially those that are corrosion resistant and high strength. Aluminum alloys offer you these qualities in these form:
AA 3003
Utilizes manganese alongside aluminum as the primary elements in the alloying process capable of cold working for strength improvement. It features decent qualities such as corrosion resistance, strength and workability commonly converted into sheets used as roofs, gutters and sidings.
AA 4043
Contains silicon in generous amounts in the alloy structure, performs decently against corrosion and commonly used in welding as filler material. This allows its use in structural application where it is used to join other metal sheets together.
AA 5005
This aluminum alloy contains magnesium in its structure and offers impeccable corrosion resistance for environmental causes. It is capable of achieving decent strength qualities allowing use in architectural applications usually as a decorative piece(s).
AA 5052
Employing trace elements of chromium alongside aluminum and magnesium, this alloy material offers good corrosion resistance and strength properties. Its structural application extends to fabricating metal sheets used as sidings and roofing, floor panels and rivets.
AA 6063
This alloy material is capable of heat treatment allowing processes such as welding and extrusion into complex shapes. It is a distinct material in architectural works like making frames for windows and doors, furniture and pipe systems.
AA 7049
This alloy is primarily worked by forging giving it impressive resistance qualities against stress application, cracking and corrosion. Parts used in structural developments can be forged from this aluminum alloy.
Examples of applications include aluminum alloy box, aluminum alloy bracket, aluminum alloy case, aluminum alloy doors and windows, aluminum alloy welding rods, aluminum alloy tripod, aluminum alloy extrusion profiles, aluminum alloy fence, etc.
Military Applications
Military applications require materials with impressive physical and mechanical qualities such as strength, corrosion resistance, thermal performance and hardness.
Common alloys:
AA 2195
Contains copper as a primary alloying element alongside elements such as lithium, magnesium, silver and zirconium. It exhibits a high strength-to-weight ratio allowing use in military jets fabricating propellant tanks.
AA 2219
You can heat treat this aluminium alloy to increase strength at the detriment of reduced ductility. Containing copper as a primary alloying element hampers corrosion resistance and weldability, however, they can be cladded or painted.
Alloy 2219 is worked on by forging and extruding resulting in fracture toughness and resistance to stress cracking from corrosion. Consequently, this aluminum alloy is utilized in supersonic military jets to make structural parts and sidings.
AA 5086
Its welding capability and decent corrosion performance make its use popular in fabricating armored vehicles used by the military.
AA 7039
Utilizing zinc as the primary alloying element, this alloy is worked by forging and is heat treatable. Its resistance qualities to stress cracking and corrosion alongside machinability make it ideal for military use as armor material.
AA 2519
Also primarily employing copper as the main alloying element, it utilizes trace amounts of silicon, magnesium, iron, zinc, titanium, manganese, and vanadium. It is utilized by the military in making aircraft armor thanks to its ballistic characteristics and resistance to stress corrosion cracking.
AA 7049
This aluminum alloy can forge highly resistant and machinable parts capable of withstanding corrosion, stress and cracking. It features severally in military industries making missile fittings and aircraft parts like cylinders for landing gears.
Examples of applications include aluminum alloy bullets, aluminum alloy for war ship building, aluminum alloy in fighter jets, etc.
Medical Applications
An important consideration for aluminium alloys used in medical applications is being contamination free and thus highly corrosion resistant. Some of the aluminum alloys you find utilized in the medical field are listed thus:
AA 3004
With magnesium content in its structure, it can tolerate cold working resulting in low ductile but high strength tempers. Its workability, decent strength and resistance to corrosion allow use in making sterile containers for medical storage.
AA 7068
Utilizes zinc as an alloying element making it a high strength alloy comparable to steels and capable of heat treatment. Its strength and chemical resistance allows for its use in the manufacture of medical devices like prosthetics.
Common examples include aluminum diagnostic equipment, aluminum cabinets, aluminum surgical equipment, etc.
Other applications:
- Sport and recreational activities where we have aluminum bike frames, aluminum alloy baseball bats, aluminum alloy bikes, aluminum alloy scooter base, etc.
- Home appliances include aluminum alloy cookware, aluminum alloy dryer drum, aluminum alloy folding table, aluminum alloy mirror
- Aluminum alloy jewelry, aluminum alloy pan, aluminum alloy heat sink, etc.
Bonus FAQs
1. How does alloy steel vs aluminum alloys compare?
The following table summarizes the comparison between alloy steel and aluminum alloy.
Property | Alloy Steel | Aluminum Alloy |
Composition | Contains Iron and Carbon as the main alloying elements. Others elements used include: manganese, nickel, chromium, molybdenum, vanadium, silicon and boron. | Contains Aluminum alongside a primary alloying element such as copper, zinc, magnesium, manganese, silicon, nickel, and iron. |
Strength | Stronger reaching a UTS of 965 MPa | Relatively strong with lower UTS at 710 MPa |
Corrosion Resistance | Less resistant to corrosion | Highly resistant to corrosion |
Weight | Heavy with a larger density | Light with lower density |
Thermal Conductivity | Poor thermal conductor | Good thermal conductor |
Malleability | Low malleability at room temperature | Highly malleable at room temperature |
2. Does Aluminum Alloy Rust?
No. Aluminum is a non-ferrous element that does not rust. Instead, it is highly corrosion resistant forming a protective layer over its surface when exposed.
3. How does Alloy Aluminum compare to Copper Alloy?
A comparison is made between alloys of copper and aluminum in the following table:
Property | Copper Alloy | Aluminum Alloy |
Melting Point | Very high at around 1,085 oC | Comparatively low at around 660 oC |
Thermal and Electrical Conductivity | Excellent | Moderate |
Ductility | Highly ductile | Comparatively lower |
Malleability | Higher | Lower |
4. Is Aluminum alloy magnetic?
Aluminum alloys are naturally not magnetic but they display paramagnetic qualities when subjected to a magnetic field.
5. How does magnesium alloy compare to aluminum?
A summary on the comparison between magnesium alloy and aluminum alloy is tabulated below:
Property | Magnesium Alloy | Aluminum Alloy |
Density | Less dense | Comparatively higher density |
Melting Point | Low boiling point | Higher than magnesium alloys |
Corrosion Resistance | Moderate | Excellent |
Thermal Conductivity | High thermal conductivity | Comparatively lower |
6. How does aluminum and brass alloys compare?
Property | Brass Alloy | Aluminum Alloy |
Composition | Main alloying element include copper and zinc | Contains aluminum alongside elements like copper, magnesium, silicon, manganese, nickel, zinc and iron. |
Density | Higher at about 8.53 g/cm3 | Lower at about 2.7 g/cm3 |
Yield Strength | Less stronger at 95 MPa | Comparatively stronger at about 240 MPa |
Melting Point | Higher at about 950 oC | Lower at about 660 oC |
Thermal Conductivity | 150 W/(m.K) | 120 W/(m.K) |
7. What is Unique about NASA 398 aluminum alloy?
NASA 398 aluminum alloy is an aluminum-silicon alloy that is highly ductile with outstanding strength performance and hardness. It displays impressive resistance to high temperatures reaching 400 oC.
NASA 398 aluminum alloy is utilized in automotive engines as cylinder blocks and pistons. They are less resistant to wear and their low thermal coefficient of expansion reduces distortion at elevated temperatures.
8. How does scandium alloy vs aluminum alloy?
Scandium alloys exhibit impressive strength when compared to aluminum alloys with good temperature performance. When you combine scandium with aluminum alloy grades such as AA 5000 you achieve materials with higher yield strengths.
9. Which is the strongest aluminum alloys?
AA 7075 displays the greatest strength performance among commercial aluminum grades with an ultimate tensile strength reaching over 570 MPa. This makes it superior even in comparison with some mild steels.
A summary comparing the ultimate tensile strengths of aluminum alloy grades is tabulated below:
Aluminum Alloy Series | Tensile Strength (Ultimate) |
1000 Series | 45.0 – 205 MPa |
2000 Series | 172 – 670 MPa |
3000 Series | 90.0 – 295 MPa |
4000 Series | 110 – 427 MPa |
5000 Series | 110 – 590 MPa |
6000 Series | 89.6 – 565 MPa |
7000 Series | 70.0 – 750 MPa |
Conclusion
As you can see, aluminum alloy plays an integral role in modern engineering applications. However, you must choose an appropriate alloy for the aluminum, select the best fabrication technique and finishing.
For all your aluminum alloy fabrication processes, KDM offers perfect solution for all your needs.