Do you know the sheet metal fabrication industry may grow by 3.52 billion USD in 2023?
You can benefit from this significant growth by adopting cost-effective, accurate and modern fabrication technologies. Additionally, you must choose a suitable material, focus on quality, application and costs, to mention a few.
Keep reading:
Chapter 1: What Is Sheet Metal Fabrication?
Fabrication refers to various processes or techniques you will use to transform sheet metal into valuable structures or products.
For example:
You may cut, bend or weld sheet metal to make a structure. Alternatively, you can punch, bend and drill to make a different structure.
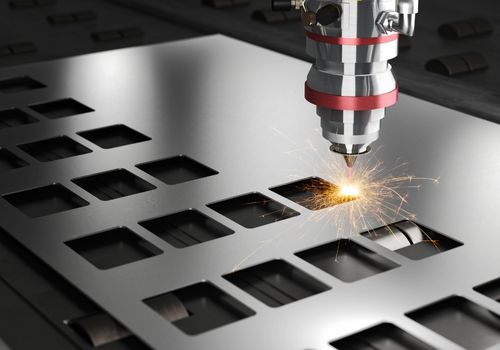
Chapter 2: Benefits Of Sheet Metal Fabrication
Nearly 97% of industries use sheet metal fabricated parts. It is due to the numerous benefits these parts offer.
However, you can only enjoy these benefits by choosing the correct fabrication technique, tool and material. You will learn more about this shortly.
Here is why you should choose fabricated metal parts:

It is a Versatile and Adaptable Process
You can fabricate virtually all sheet metal types. Besides, you can make various part designs and shapes – from complex to simple sheet metal parts.
Easy to Control Cost
Cost is an essential parameter in any sheet metal fabrication process.
In metal fabrication, you can control virtually all parameters determining the overall project cost. For instance, you can choose an affordable sheet metal fabrication technique, material or surface finish.
You Can Produce a Range of Parts and Components
Whether you want simple or complex parts, fabricating sheet metals offer unlimited possibilities. Additionally, you can make small to large sheet metal parts.
Easy to Control Quality
Choosing the best metal fabrication technique, and working with a highly trained team, will guarantee quality parts.
Additionally, you can opt for a precision sheet metal fabrication process. Here, you will use CNC machines, which produce accurate parts.
You have Competitive Edge
Fabricating sheet metal will give you a competitive edge. You can control the quality, features and cost of the entire project.
It is Effective and Efficient
It is easier to optimize the fabricated sheet metal part designs. As a result, you increase efficiency.
Additionally, increasing production capacity will be an easy process.
In short, fabricating sheet metals offer many benefits in modern industries.
Chapter 3: Sheet Metal Fabrication Process
Fabricating sheet metal parts can be a simple or complex process. It will depend on the sheet metal part design.
However, the critical stages in the entire process remain the same.
Let’s take a look at some of the key processes:
Design Sheet Metal Part
Design is the first step in the sheet metal fabrication process. There are many CAD software that will help in the design process.
Whether you opt for in-house or outsourcing sheet metal parts fabrication, a good design will translate into better components.
Additionally, you must pay attention to the following:
- Design for manufacturability (DFM) will help you evaluate the viability and practicality of fabricating sheet metal parts.
- Sheet metal prototype fabrication – you will make a sample product for testing, quality verification and approval before mass production starts.
Cutting Sheet Metal
Sheet metals are available as coiled strips or flat pieces. Therefore, you will cut the section you need for subsequent processes.
You may also refer to cutting sheet metal as a subtractive fabrication.
You will choose the cutting technique depending on the sheet metal gauge, part design, material type or available resources.
Let’s look at the standard cutting techniques:

Laser cutting is suitable for precision sheet metal fabrication. The machine uses an intense laser beam to vaporize sheet metal parts – hence cutting accurate pieces.
Some notable aspects about laser cutting sheet metal are:
- High accuracy and energy efficiency
- Suitable for medium to thin sheet metal gauge
- Cutting or penetrating hard sheet metals can be a challenge
More Resources:
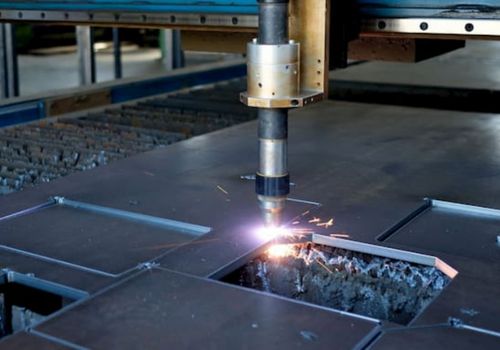
In a plasma cutter, an ionized gas cuts the sheet metal parts. Usually, the ionized gas has an extremely high temperature.
The material will melt by directing the gas stream on the sheet metal.
Ideally, the process involves the formation of an electric arc.
Even as you choose plasma cutting sheet metal, it is worth noting the following:
- The process is powerful
- The degree of accuracy is less than Waterjet cutting sheet metal or laser cutting sheet metal
- It can cut sheet metals with thick gauge
More Resources:
Understanding Arc Plasma Cutting
Waterjet Cutting Sheet Metal
A mixture of high-pressure water jet and abrasive materials cut the sheet metal. You can cut sheet metal into various shapes and sizes.
Waterjet cutting is a perfect option for sheet metals with low melting points.
Remember, Waterjet sheet metal cutting does not produce heat.
More Resources:
Cutting Sheet Metal With Saw
You can use a hack, circular, jigsaw, band, or table saw to cut sheet metal. Of course, these are the most common options for DIY projects.
This sheet metal cutting technique is suitable for small to large projects. You can handle simple to complex projects.

More Resources:
Although these are some of the most common techniques you will use to cut sheet metal materials. Others may include:
- Drilling sheet metal – You will remove sections of the materials by creating holes in sheet metal.
- Milling sheet metal – a rotating cutter will remove unwanted sheet metal parts.
- Grinding sheet metal – a grinder gradually removes unwanted sheet metal sections.
Additionally, you can use punching, piercing, perforating and blanking. They may also form part of sheet metal cutting processes.
After cutting the sheet metal, you can transform the section into different shapes and designs.
How can you achieve this?
Sheet Metal Deformation Or Forming Sheet Metal
Deformation or forming involves transforming the sheet metal into different shapes and designs. Again, there are various techniques you will use, such as:
Sheet Metal Bending Process
Sheet metal bending is the plastic deformation of a workpiece over a specific axis. As a result, it changes the sheet metal’s geometrical shape.
You may consider these options to bend sheet metal parts:
- V bending sheet metal
- Bottoming sheet metal
- Coining sheet metal
- Air-bending sheet metal
- Wipe bending sheet metal
- Roll bending sheet metal
- Rotary draw bending sheet metal
- Step-bending sheet metal
Closely related to sheet metal bending is sheet metal folding.
Whichever technique you choose, the final part will have unique shapes and properties. Therefore, you must understand how every process works.
By the end of this process, you will have unique sheet metal with a specific shape.
More Resources:
Sheet Metal Bending Parts (Complete Guide)
Factors to Consider When Bending Sheet Metal Parts
Sheet Metal Folding Vs Bending
Apart from the bending process, other fabrication techniques you may use to deform sheet metals are:
- Spinning sheet metal will help you form axially symmetrical round metal parts. A lateral force transforms the material into a suitable shape as the workpiece rotates on the spindle.
- Hydroforming sheet metal – using a special die and pressure, you can deform sheet metal into different shapes.
- Embossing sheet metal creates raised or sunk parts on sheet metal surfaces. It is a popular marking technique.
More Resources:
At this point, you can have a finished sheet metal fabricated part. Otherwise, you should proceed to other processes such as:
- Sheet metal parts assembly
- Apply surface finish on sheet metal parts
You will learn more about these two shortly.
Chapter 4 Sheet Metal Assembly
A sheet metal part may have the following:
- A single unit/one piece
- Different parts joined together
If your part has more than one unit, sheet metal assembly is critical.
Sheet metal assembly involves joining different sections to form a whole part. Therefore, the type of sheet metal assembly technique will depend on:
- Type of joint you need – whether permanent or temporary
- Strength of the joint
- Type of material
- Sheet metal part design
- Sheet metal part application, amongst others.
Specifying the type of assembly technique during the design stage is essential.
Some of the most common sheet metal parts assembly techniques include:

You can use bolts and nuts to assemble sheet metal parts. Alternatively, you can use screws.
You can quickly assemble and disassemble the fabricated sheet metal parts with fasteners.
More Resources:
Welding Sheet Metal Parts
Welding sheet metal parts are perfect for permanent and strong joints. Depending on the type of material, you can choose any of the following welding techniques:
- Fusion welding
- Arc welding – some of the most common options include gas metal arc welding, shielded metal arc welding, submerged arc welding, tungsten inert gas, electro-slag welding, flux cored arc welding, arc stud welding, electro-gas welding, atomic hydrogen welding and carbon arc welding
- Gas welding – available options are air-acetylene welding, oxy-acetylene welding, oxy-hydrogen welding and pressure gas welding
- Resistance welding – available options include resistance spot welding, resistance seam welding, projection welding, percussion welding, flash welding and upset welding
As you can see, there are many sheet metal welding techniques to choose from.
Closely related to welding are soldering and brazing. In these techniques, you will use metal filler to weld.
More resources:
Riveting Sheet Metal Parts
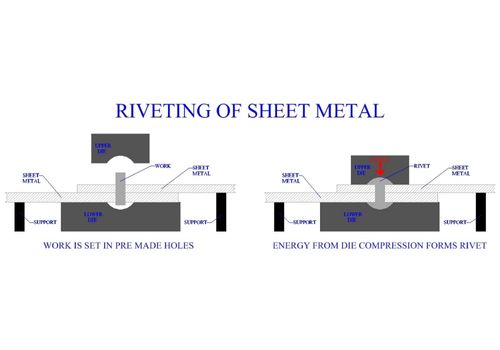
Riveting forms durable and robust joints. It is a perfect option for parts subjected to fluctuating temperature and pressure.
Some common designs are solid rivets, tubular rivets, self-piercing rivets, blind rivets, and flush rivets.
More Resources:
Apart from these sheet metal assembly techniques, others include;
- Tongue and groove sheet metal assembly
- Adhesive bonding sheet metal assembly
- Assembling sheet metal using hemming
- Snap fits assembly technique
- Using clinching and tabs to assemble sheet metal
Whichever process you choose, the final sheet metal part should be robust, durable and reliable.
Chapter 5 Surface Treatment for Sheet Metal Parts
After fabricating sheet metal parts, and the subsequent assembly process, it is time to apply surface treatments.
Typically, these surface treatments for sheet metal parts will:
- Improve aesthetic appeal
- Improve corrosion resistance and hardness
- Add extraordinary features on the sheet metal part
Depending on the sheet metal part and materials, you may consider many surface treatment options.
Let’s have a quick overview:

Electroplating Sheet Metal Parts
A thin metallic coating will form on the fabricated sheet metal part during electroplating.
It is one of the most common surface treatment options. In most cases, electroplated nickel and electro-galvanizing are the most common.
Electroless Plating
Unlike the electroplating process, this process does not require electricity.
Anodic Oxidation
It is a perfect choice for fabricating aluminum and titanium parts. Here, a thin film will form on fabricated sheet metal parts, thereby:
- Improving aesthetic appeal
- Preventing corrosion on metal surfaces
- Improving wear resistance
Hot Dipping
You will dip fabricated sheet metal parts in the desired metallic coating. These can be lead, tin, aluminium or zinc.
As a result, it forms a coating which is:
- Corrosion resistant
- Better aesthetic appeal
Chemical Treatment
Through a series of chemical reactions, chemical treatment will form a thin film on the fabricated sheet metal part. It is a popular process for:
- Sheet metal part coloring
- Priming sheet metal surface before painting
- Protecting surface from corrosion
Vacuum Plating
Some of the most common techniques which use this technology include:
- Ion plating and implantation
- Vacuum vapour deposition
- Sputtering
Thermal Spraying
In this technique, you will melt the coating material and apply it to the fabricated sheet metal components.
The surface treatment will protect the metal part against high temperature and friction.
Powder Coating
You will spray powder coating on sheet metal parts. The sheet metal will absorb the powder.
Next, you will bake the sheet metal part at a reasonable temperature for a powder to flow on the entire surface.
Painting
Whether you opt for wet or liquid painting, it makes the surface corrosions resistant and improves aesthetic value.
Additionally, you can use silkscreen printing, abrasive blasting or chromate coating.
As you can see, many surface treatments for sheet metal parts exist. Always talk to a professional sheet metal fabricator for advice on suitable surface treatment.
More Resources:
Chapter 6: Sheet Metal Fabrication Cost
Cost is a vital element in the sheet metal fabrication process. Every sheet metal fabricator strives to find affordable solutions.
Of course, a low-cost sheet metal fabrication does not imply low-quality parts.
With these in mind, let’s look at critical aspects of controlling sheet metal fabrication costs.
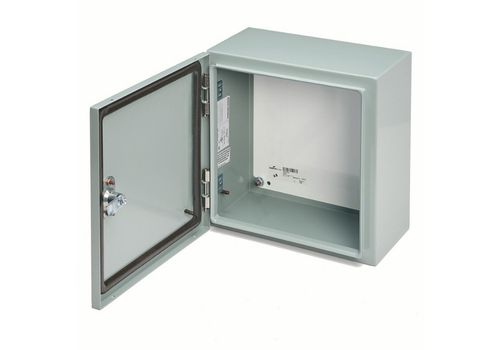
Factors Determining Cost of Sheet Metal Fabrication
Many factors determine sheet metal fabrication cost. They include:
Type of Material
First, the sheet metal types will determine how much to pay for the fabrication process. Ideally, the cost of stainless steel, aluminium, or copper varies.
Secondly, the sheet metal grade, gauge and size determine sheet metal fabrication cost estimation.
Sheet Metal Fabrication Technique
The fabrication technique will determine sheet metal fabrication cost. For instance, the cost of cutting sheet metal with a laser machine is different from a hand saw.
Of course, this also goes hand in hand with labor.
Nature Of Sheet Metal Parts
Complex parts are more challenging to fabricate than simple designs. It is because you will require sophisticated technology to fabricate the sheet metal parts.
Again, the degree of tolerance and accuracy will also determine the sheet metal fabrication prices.
Final Surface Finish and Assembly
The final finish on the sheet metal part will determine the overall cost during the fabrication process.
Of course, the same applies to the sheet metal assembly process.
How to Reduce Sheet Metal Fabrication Cost
There is no specific formula to reduce the cost of fabricating sheet metal. However, the following measures will reduce the total cost:
Use Sheet Metal Fabrication Price Calculator
It will help you determine sheet metal fabrication cost estimation. With this information, you can adopt special measures that cut costs.
Flexibility in Sheet Metal Part Design Is Critical
Remember, changing two or three dimensions can significantly impact the total sheet metal fabrication cost.
Additionally, adopting in-house tooling can also help reduce fabrication costs.
Work Closely With Experienced And Reputable Sheet Metal Fabricators
A sheet metal fabricator with experience will help you reduce the over cost. They can help redesign, choose appropriate fabrication techniques, suggest alternative finishing, etc.
Other ways to reduce costs are:
- Use readily available sheet metals
- Go for simple designs where you can
- Always conduct design for manufacturability (DFM)
- Finishing options should cut cost
- Go for tight tolerance when necessary
Although websites like a homeowner may give sheet metal fabrication prices as $100 for low and $5,000 – they may be misleading.
Contact the sheet metal fabricator if you want accurate estimations.
More Resources:
Cost of Fabricating Sheet Metal
Ways to Cut Fabricating Sheet Metal Cost
Chapter 7: Sheet Metal Fabrication Machine
There are many sheet metal fabrication machine designs.
However, you may require specialised machines whenever there are specific process requirements, such as precision sheet metal fabrication. In this case, you will use CNC machines for sheet metal fabrication.
Some of the most common machines for fabricating sheet metal include:

Figure 10 Sheet metal bending machine
- Cutting machines such as laser cutting machines, Waterjet cutting machines, plasma cutters,
- Sheet metal banding machines – press brakes help in the sheet metal bending process
- Plate rolling machines – you will use the equipment to form conical or round sheet metal parts
- Shears – they help cut sheet metal sheet
- Punching machine – turret punching help in the sheet metal punching process
- Lathe machines can perform various functions such as drilling sheet metal, boring sheet metal, spinning sheet metal, and cutting sheet metal, amongst others.
- Milling machines – they remove unwanted sheet metal parts
- Welding machines – you will use the equipment to join different pieces of sheet metals
- Riveting machine
In short, every metal fabrication process will require a unique machine. Therefore, the metal fabrication machine types depend on the fabricators’ capability.
Chapter 8: Sheet Metal Fabrication Calculator
A sheet metal fabrication calculator is an interactive software for estimating various parameters when fabricating metal parts.
Currently, no standard sheet metal fabrication calculator is 99.9% accurate. The available calculators only give estimated values.
Sheet metal bending calculator is the most popular software in the industry. They come in different configurations.
With this calculator, once you input sheet metal thickness and inside radius, you can get the following:
- K-factor
- Y-factor
- Neutral axis offset
Again, once you input the sheet metal bending angle, you will get:
- Bending allowance
- Arc length
Additionally, among the other sheet metal fabrication calculators are:
- Bend allowance calculator
- Bending spring-back calculator
- V-bending and wipe force calculator
Interestingly, developers are working on a sheet metal fabrication cost calculator. Well, I recommended contacting a sheet metal fabricator for accurate cost estimates.
More Resources:
Sheet Metal Fabrication Calculator
Sheet Metal Bending Calculator
Chapter 9: Sheet Metal Fabrication Material
There are many types of sheet metal types and grades. Typically, the sheet metal fabrication material type will depend on the intended application.
Let’s look at some of the most common options:
Aluminum Sheet Metals
Aluminum is known for its lightweight and excellent strength. It is suitable for low-temperature applications.
Additionally, you can quickly fabricate aluminum sheet metal.
More Resources:
Steel Sheet Metal
Steel sheet metals are available as stainless steel, galvanized steel and carbon steel. All the steel alloys are easy to fabricate.
Besides, they form excellent sheet metal parts and components. They have excellent mechanical and chemical properties.
More Resources:
Stainless Steel Sheet Fabrication
Mild Steel Sheet Metal Fabrication
Galvanized Sheet Metal Fabrication
Magnesium Sheet Metal
Fabricating magnesium sheet metal will be the best option where you need stiff and low-density material.
More Resources:
Brass Sheet Metal
Brass sheet metal is known for being lightweight, having high tensile strength and excellent corrosion resistance.
More Resource:
Bronze Sheet Metal Fabrication
Bronze sheet metal is a low melting point material. However, it is stronger than copper sheet metal.
More Resources:
Copper Sheet Metal
Copper sheet metals are electrically conductive and corrosion-resistant. They are easy to fabricate.
More Resources:
Copper Sheet Metal Fabrication
Titanium Sheet Metal Fabrication
Titanium sheet metal is easy to fabricate. It can withstand extremely high temperatures.
Additionally, they have a good weight ratio, toughness and excellent corrosion resistance.
More Resources:
Titanium Sheet Metal Fabrication
You can fabricate virtually all sheet metals.
However, you should know the physical and chemical properties before fabricating any sheet metal. With this information, you will choose suitable fabrication techniques.
Chapter 10: Sheet Metal Fabrication Application

Today, every industry uses at least one or two sheet metal fabricated parts.
Whether you want small, large, simple or complex parts – fabricated sheet metal parts have dominated virtually all industries.
Let’s look at some examples:
- Aerospace industry – aeroplane body parts
- Building and construction – roofing parts, doors, gutters, windows, etc.
- Agricultural – irrigation equipment, storage cabinets,
- Electronics – electrical enclosure, electronic casing, brackets, phone parts
- Oil and gas industry – storage tanks, stairs, etc.
- Medical sector – medical instruments, plates, implants,
- Automotive industry – vehicle body and related parts
You can make virtually anything by fabricating sheet metal.
Chapter 11: How to Check the Sheet Metal Parts Quality
Quality inspection and control are essential aspects in fabricated sheet metal parts.
Typically, the quality inspection process varies depending on the sheet metal part you are fabricating. Remember, every industry has unique quality standard specifications.
For example, quality requirements for welding aeroplane body parts differ from steel doors.
Let’s look at some vital quality inspection criteria in sheet metal parts:
- Check sheet metal material quality – you can use the cupping test, tensile test, fatigue, hardness test, etc.
- Examine sheet metal part thickness
- Ensure the fabrication process adheres to acceptable standards – for instance, ISO 1461 for hot dig galvanization, ASTM standards for sheet metal welding, etc.
- Surface finish quality matters – check for any defects or possible inconsistency
- Ensure the joints are as per specification
- Check the sheet metal fabricating company quality procedures
- Non-destructive testing such as AS9102 First Article Inspection Report (FAIR) and Geometric Dimensioning and Tolerancing (GD&T) are also critical
- Review third-party quality inspection report
Quality testing should also focus on fabrication equipment and processes. This way, you can easily predict the quality of the final sheet metal fabricated part.
Chapter 12: KDMFAB Capabilities Of Sheet Metal
Over the years, KDMFAB has remained a global leader in sheet metal fabrication parts. Through our experienced engineers and technicians, we offer unlimited possibilities in the sheet metal fabrication industry.
At KDMFAB, fabricate small, large, simple and complex sheet metal parts. We can handle a range of fabrication processes for sheet metal, such as:
- Sheet metal cutting – a range of cutting options such as shearing, Waterjet, plasma and laser cutters are available
- Sheet metal welding – you can use robotic welding for high consistency and accuracy. We use laser welding, MIG welding and TIG welding.
- Sheet metal forming – our brake bending machine guarantees a high level of accuracy
- Sheet metal shrinking – KDM metal shrinking machines guarantee zero dents
With the CNC machines, KDM ensures high precision and repeatability.
The KDMFAB team will help you choose the best options for sheet metal surface finish.
Talk to us now for competitive prices on fabricated sheet metal parts. We support OEM clients too.
Conclusion
It would be best if you worked with a professional sheet metal parts fabricator. They will help you get quality sheet metal parts and affordable prices.
Contact us if you have any questions about fabricating sheet metal parts.